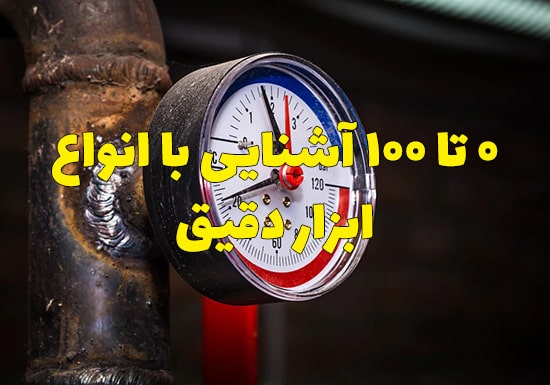
۰ تا ۱۰۰ آشنایی با انواع ابزار دقیق در پایپینگ
ابزار دقیق مجموعهایی از ابزارآلات است که به منظور نظارت، اندازهگیری و کنترل یک فرآیند مورد استفاده قرار میگیرند. امروزه استفاده از ابزار دقیق یک جزء مهم و جدا نشدنی از فرآیندهای صنعتی میباشد. بدون استفاده از سیستمهای ابزاردقیق، نمیتوان محصولات را در حجم گستره و کیفیت یکسان تولید کرد. ما در این مقاله قصد داریم که با انواع ابزار دقیق و کارایی آنها در صنعت پایپینگ آشنا شویم و تأکید این آموزش بر روی ابزار دقیقهایی است که در صنعت نفت و گاز مورد استفاده قرار میگیرند.
در تمام فرآیندهای تولیدی نیاز است که برای رسیدن به حداکثر کیفیت و حداقل ضایعات در تولید یک محصول، کنترل ابتدا تا انتهای فرآیند ضروری است. به عنوان یک مثال ساده در نظر بگیرید برای تولید یک غذای خوشمزه و دلچسب لازم است که شما به درستی موارد شامل: مقدار اضافه کردن مواد اولیه، زمان اضافه کردن، مقدار پخت هر کدام و زمان کلی پخت را انجام بدهید. حال اگر این مثال را برای فرآیندهای صنعتی تولیدی نظیر پالایشگاه ارائه کنید باید در نظر داشت که تولید مواد پتروشیمی تقریباً شبیه به همین مثال ارائه شده است با این تفاوت که در این فرآیندها خطرات جانبی ناشی از عدم رعایت صحیح قوانین به شدت بالاست؛ پس با این مثال کاملاً مشخص شد که برای رسیدن به یک محصول باید آن را لحظه به لحظه کنترل کنیم که انجام این مهم بدون استفاده از ابزار دقیق غیر ممکن است.
پیشینهی استفاده از ابزارآلات کنترل که ابزار دقیقهای امروزی را به وجود آوردهاند تاریخ طولانی دارد. از نمونهی از ابزار دقیق گذشته، دستگاه گریز از مرکز جمیز وات برای کنترل دور ماشین بخار است که به انگلیسی با نام Centrifugal Governor شناخته میشود. از این وسیله جهت کنترل دور ماشین بخار وات استفاده میشد. در ویدئوی زیر نحوهی کار این ماشین را مشاهده میکنید. در این ماشین که از یک مکانیزم حرکت رفت و برگشتی (خطی) استفاده میکند با افزایش سرعت محور محرک که از طریق چرخدندهی جناغی به ماشین وصل شده است گویهای کروی متصل به میله راهنما که از طریق دو بازو به یک بلبرینگ خطی متصل شدهاند به علت افزایش نیروی گریز از مرکز به بالا هدایت میشوند و همراه با بالا رفتن آنها سبب انسداد شیر پروانهایی شده که جریان تزریق بخار به ماشین بخار را کم میکند و به صورت مشابه اگر سرعت ماشین کم شود گویها پائین میافتند و با تزریق بخار به سیستم سرعت ماشین بالا میرود.
روش کنترل ابزار دقیق
دستگاههای اولیه اتوماسیون با استفاده از مکانیزمهای مکانیکی، فرآیند را کنترل میکردند اما امروزه با کمک سیستمهای جدید کنترل مبتنی بر ریز پردازنده و رایانه و بکارگیری الگوریتمهای فازی لاجیک (منطقی) یا شبکههای عصبی مسائل کنترل تجهیزات صنعتی بکار رفته در صنایع مختلف شامل: فضایی، نظامی پالایشگاهی بخوبی قابل حل میباشد.
سیستم کنترل ابزار دقیق
سیستم کنترل ابزار دقیق یا به انگلیسی Instrument Control System، از سه قسمت اساسی تشکیل شده است که عبارتند از:
۱) اندازه گیرها (Measuring Instrument)
۲) کنترلکننده (Control System)
۳) سیستم کنترل نهایی (Final Control Device)
۱) اندازه گیرها
اندازه گیرها اولین بخش وظیفه یک ابزار دقیق را انجام میدهند آنها با نظارت بر فرآیند، پارامترهای موجود را اندازهگیری میکنند و به صورت کمی اعلام میکنند و نتیجه را به بخش بعدی یعنی کنترلکننده، برای انجام اقدام بعدی ارسال میکند. دستگاه اندازهگیری شامل سه بخش اصلی سنسور (Sensor)، ترانسدیوسر (Transducer) و ترانسمیتر (Transmitter) میباشد که هر کدام را در ادامه توضیح میدهیم.
الف) سنسور
سنسور یا به انگلیسی Sensor، وسیلهایی است که به منظور سنجش یک پدیده فیزیکی مانند: حرکت، حرارت، فشار، مغناطیس و غیره مورد استفاده قرار میگیرد. سنسور وضیعیت پارامتر اندازهگیری شده را به صورت سیگنال ارسال میکند.
ب) ترانسدیوسر
ترانسدیوسر یا به انگلیسی Transducer، یک وسیلهی مبدل است که انرژی را از شکلی به شکل دیگر تبدیل میکند. ترانسدیوسر، سیگنال را در یک شکل انرژی به سیگنالی در شکل دیگر تبدیل میکند که برای کنترلکننده قابل درک باشد.
ج) ترانسمیتر
ترانسمیتر یا به انگلیسی Transmitter، وسیلهای است که یک سیگنال خروجی ترانسدیوسر را به سیگنال استاندارد قابل انتقال که به صورت امواج رادیویی تبدیل میکند و آن را به آنتن منتقل میکند.
۲) کنترلکننده
کنترلکننده یا به انگلیسی Control System، سینگال رسیده شده از سنسور را با نقطه تنظیمی (Set Point) مقایسه میکند و فرمان مورد نیاز را به سیستم کنترل نهایی جهت کنترل فرآیند و رسیدن به نقطهی تنظیم مورد نظر را ارسال میکند.
۳) سیستم کنترل نهایی
سیستم کنترل نهایی یا به انگلیسی Final Control Device، مجموعه تجهیزاتی هستند مانند: شیرهای کنترل (کنترل ولو)، موتورها، هیترها و غیره که فرامین را از قسمت کنترلکننده دریافت میکنند و با اجرای آن، پارامترهای اندازهگیری شده را به سطح مطلوب میرسانند.
ابزار دقیقهای اندازهگیری فشار، دما، فاصله و سطح
در ادامه این مقاله ابزار دقیقهای اندازهگیری فشار، دما، فاصله و سطح را بحث خواهیم کرد و نحوهی انجام آن را بررسی خواهیم کرد.
ابزار دقیقهای اندازهگیری فشار
۱) مانومتر
مانومتر یا به انگلیسی Manometer، قدیمیترین وسیلهی اندازهگیری فشار بوده است. مانومتر یک لولهی U شکل است که داخل آن با یک سیال مانند جیوه پر شده است و دو فشار مختلف به دو طرف آن اعمال میشود. این اختلاف فشار باعث جابجایی مایع در لوله میگردد که با اندازهگیری این اختلاف سطح میتوان فشار مورد نظر را به دست آورد. استفاده از مانومتر در ابزاردقیقها برای سنجش فشار، کاربرد محدودی دارد.
۲) بوردن تیوب
بوردن تیوب یا به انگلیسی Bourdon Tube، دارای یک لولهی پیچیده شده از جنس فلز فنر (قابل ارتجاع) است که یک طرف آن مسدود و طرف دیگر آن به ورودی گاز متصل شده است که زمانی که گاز به داخل این لوله هدایت میشود لوله به سمت شعاع خارجی خود باز میشود که سنجش میزان باز شدگی نسبت به مقدار اولیه، میتواند مقدار فشار را نشان دهد. بوردن تیوبها در شکلهای مختلف تولید میشوند که در ادامه یک نمونهی آن را مشاهده میکنید.
۳) دیافراگم
دیافراگم یا به انگلیسی Diaphragm، یک مبدل مکانیکی فشار میباشد که میتواند تغییرات اندک فشار را نشان دهد. فشار سنج دیافراگمی دارای یک صفحه تخت انحنا دار است که وقتی جریان سیال از یک سمت به آن نیرو وارد میکند باعث بالا آمدن عقربه متصل به آن شده و در نتیجه فشار سال را نشان میدهد. فشار سنج دیافراگمی نسبت به بوردن تیوب علاوه بر اینکه تغییرات اندک فشار را میتواند نشان دهد در فشارهای زیاد قابل استفاده است و همچنین پایداری بالایی دارد.
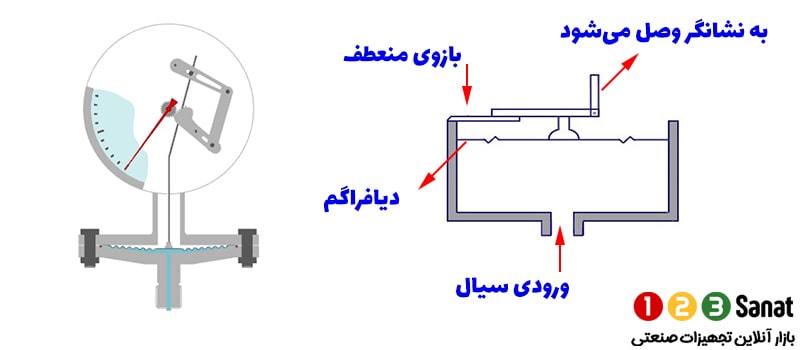
۴) دمنده
دمنده یا به انگلیسی Bellows، نوعی دیگر از ابزار دقیق سنجش فشار است که از یک لولهی آکاردئون تشکیل شده است که زمانی که سیال پر فشار به آن وارد میشود طول آن افزایش پیدا میکند و در نتیجه آن به عقربه متصل به آن نیرو وارد میکند و مقدار فشار سیال مشخص میشود.
۵) اندازه گیرهای پیزو الکتریکی فشار
چهار مورد گفته شده در بالا روشهای مکانیکی سنجش فشار بودهاند اما اندازه گیرهای پیزو الکتریکی فشار جزء روشهای الکترونیکی سنجش فشار میباشند. پیزوالکتریک قابلیت تبدیل انرژی الکتریکی را به انرژی مکانیکی یا برعکس را دارد.
زمانی که پیزو الکتریک در فشار سنج تحت فشار قرار میگیرد متناسب با آن فشار، اختلاف پتانسیلی را ایجاد میکند که آن اختلاف پتانسیل برای نمایش فشار استفاده خواهد شد.
ابزار دقیقهای اندازهگیری دما
۱) ترموکوپل
ترموکوپل از دو فلز غیر هم جنس تشکیل شده است که از یک سر به هم متصل شدهاند. اساس کار ترموکوپل ابزار دقیق بر پدیده اثر سیبک به انگلیسی Seebeck Effect است. اثر سیبک بیان میکند زمانی که دما در یک سمت با دما در سمت دیگر تفاوت داشته باشد یک جریان الکتریکی در مسیر برقرار میشود.
نحوه کار آن به این صورت است که انتهای دو سر دو فلز غیر هم جنس که به یکدیگر وصل شدهاند در محل مورد نظر برای سنجش دما قرار میگیرد که به آن نقطه گرم یا Hot Junction گفته میشود و دو سر دیگر که به آن نقطه سرد یا Cold Junction گفته میشود به داخل ترموکوپل میرود تا دستگاه با مدار الکتریکی و بررسی جریان الکتریکی، مقدار دما را مشخص کند.
ترموکوپلها قابلیت سنجش دما را در طیف گسترهی ۲۰۰- تا ۱۵۰۰ درجه سانتی گراد را دارند. همچنین آنها وسایل اقتصادی و با دوام برای سنجش دما هستند. ترموکوپلها بر اساس نوع جنس دو فلز غیر هم جنس آن محدودهی دمایی مشخص برای سنجش دارند.
۲) دما سنج RTD
دما سنج RTD، که مخفف Resistance Temperature Detectors به معنای تشخیص دهنده مقاومت حرارتی است بر اساس سنجش تغییر مقاومت فلزات در دمای مختلف کار میکند.
با قرار دادن سنسور RTD داخل یک مدار پل و محاسبه مقاومت RTD با توجه به مدار پل از روی جدول، دمای مقاومت مربوط را پیدا میکنند. به منظور جلوگیری از خطاهای مربوط به مقاومت، سیمهای رابط را به صورت ۳ سیمه بجای ۲ سیمه تولید میکنند که در شکل زیر قابل مشاهده است.
ابزار دقیقهای اندازهگیری سطح، فاصله و ارتعاشات
۱) ارتفاع سنج غوطه وری
ارتفاع سنج غوطه وری یا به انگلیسی Displacer Level Sensor، تجهیزی است که با استفاده از اصل قانون ارشمیدوس و نیروی شناوری با اندازهگیری وزن میله غوطه ور در مایع، سطح مایع را اندازهگیری میکند.
میله غوطه ور در مایع را معمولاً به شکل استوانههای باریک و بلند میسازند تا همواره وزن میله غوطه ور از نیروی شناور بیشتر باشد تا میله در داخل مایع غوطه ور شود.
اگر به قانون برآیند نیروهای وارد بر یک جسم مروری داشته باشیم، نیروهای وارد بر یک جسم برآیند کل نیروهای وارد بر آن است. در این مسئله دو نیروی وزن و شناور به میله غوطه ور وارد میشوند. برآیند این نیروها مشخص میکند که چه مقدار سیال بالای میله قرار دارد.
با افزایش سطح مایع، به میله غوطه ور نیروی شناور بیشتری وارد میشود که از شکل زیر قابل مشاهده است. با افزایش این نیرو، مقدار برآیند نیروها تغییر میکند که با سنجش این تغییر، ارتفاع سیال مشخص میشود. میتوان توضیح داد زمانی که میله غوطه ور با سیال در تماس نباشد، سنسور مقداری برابر با وزن آن میله نشان میدهد در حالیکه اگر میله در سیال غوطه ور شود به اندازه ارتفاع ستون مایع بالای میله از وزن آن کاسته میشود که این کاهش را سنسور ثبت میکند.
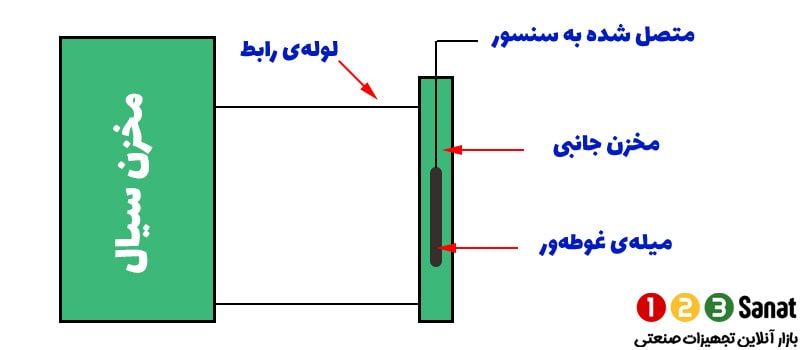
۲) ارتفاع سنج حبابی
ارتفاع سنج حبابی یا به انگلیسی Bubbler Level Sensor، با استفاده از تشکیل حباب، ارتفاع مایع را اندازهگیری میکند. برای اینکه حباب در داخل یک سیال تشکیل شود لازم است تا فشار بحرانی تشکیل حباب از فشار ستون مایع سیال بیشتر باشد. با سنجش فشار بحرانی که لازم است کمپرسور تولید کند تا حباب تشکیل شود، ارتفاع مایع را اندازهگیری میکنند.
میتوان توضیح داد زمانی که مخزن خالی از سیال باشد، هوا بدون ممانعت از انتهای خروجی هوا خارج میشود و ابزار دقیق، ارتفاع صفر را نشان میدهد و در صورت افزایش ارتفاع مایع خارج شدن حباب همراه با سختی خوهد بود که سنجش میزان مقاومت به خروج هوا میتواند ارتفاع سیال را نشان دهد.
۳) ارتفاع سنج اختلاف فشار
ارتفاع سنج اختلاف فشار یا به انگلیسی Differential Pressure (DP) Level Measurement روش دیگری برای سنجش سطح مایع است. هر مایع که داخل مخزن وجود دارد به کف آن نیروی را وارد میکند که به چگالی و ارتفاع ستون مایع بستگی دارد. لذا با تغییر سطح مایع فشار وارد شده به کف مخزن نیز تغییر میکند که با نصب ترانسمیتر فشار (Pressure Transmitter) این امکان وجود دارد که این تغییرات را به سیگنال الکتریکی یا دیجیتالی تبدیل کرد یا توسط فشارسنج آن را مشاهده کرد.
نکتهی حائز اهمیت برای خوانش سطح مایع با ارتفاع سنج اختلاف فشار این است که در مخازن ذخیره رو باز و رو بسته کمی متفاوت است.
در مخازن رو باز قسمت فشار بالای وسیلهی ابزاردقیق را به پایینترین نقطه اندازهگیری یعنی کف مخزن وصل میکنند و قسمت فشار پایین وسیله ابزاردقیق، به هوای آزاد وصل میکنند تا با سنجش اختلاف این دو ارتفاع ستون مایع بدست آید.
در مخازن رو بسته همانند مخازن رو باز، قسمت فشار بالای وسیلهی ابزاردقیق به پایینترین نقطهی اندازه گیری وصل میشود و قسمت فشار پایین هم به نقطهای بالاتر از بالاترین سطح مایع که فقط شامل گاز یـا بخـار اسـت، وصـل میشود. به این اتصال معمولاً ً Dry Leg گفته میشود. در برخی از مخازن رو بسته که ممکن است وجود میعانات بخار (Vapor Condensate) سبب بروز خطا در خوانش شود، قسمت فشار پایین وسیله ابزاردقیق را داخل قسمت بالایی مایع قرار میدهند که به این روش Wet Leg گفته میشود.
۴) ارتفاع سنج التراسونیک
امواج فراصوت یا التراسونیک کاربردهای مختلفی در صنایع مخلف دارد. از این امواج برای تشخیص عیوب [ برای اطلاعات بیشتر مقاله سیر تا پیاز تست التراسونیک UT را مطالعه کنید ]، ایجاد تصویر اسکن درون ماده و غیره استفاده میشود. در این بخش با کاربرد التراسونیک در سنجش ارتفاع سطح مایع آشنا خواهیم شد.
ارتفاع سنج التراسونیک یا به انگلیسی Ultrasonic Level Transmitter، یک روش اندازهگیری سطح مایع بدون تماس با آن است که برای سنجش مایعات بسیار داغ، خورنده مناسب است. امواج فرستاده شده توسط فرستنده وقتی که دچار تغییر محیط میشوند منعکس میشوند و امواج منعکس شده توسط گیرنده دریافت میشوند که با محاسبه زمان سفر موج و داشتن سرعت موج در محیط، مسافت طی شده بدست میآید که این مسافت همان ارتفاع ستون مایع است.
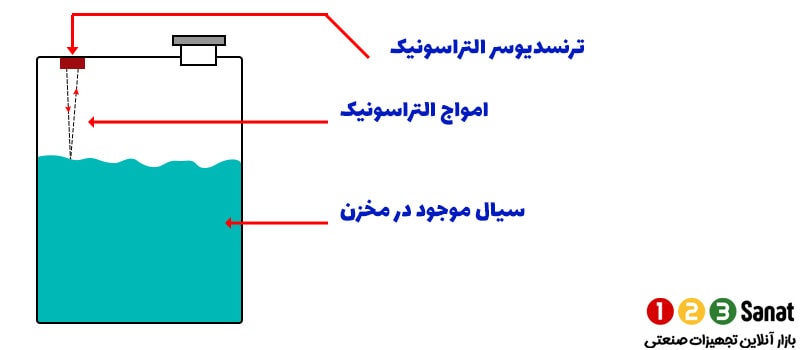
۵) اندازه گیری ارتعاشات با پراکسیمیتر
تجهیزات ترسدیوسرهای پراکسیمیتی یا به انگلیسی (Proximity Transducer System)، با استفاده از جریان گردابی [برای اطلاعات بیشتر مقالهی ۰ تا ۱۰۰ تست ادی کارنت، جریان گردابی ET را مطالعه کنید] یک اختلاف پتانسیل در حد فاصل نوک پروب (Probe) و سطح رسانا ایجاد میکند که برای کاربردهای مختلف که یکی از آنها اندازهگیری ارتعاش است استفاده میشود. به عبارت دیگر اختلاف پتانسیل ایجاد شده توسط پروبها، به فاصلهی بین محور و پروب بستگی دارد که با بررسی این اختلاف پتانسیل کارهای مختلفی را میتوان انجام داد که در اینجا به بررسی دو مورد یعنی اندازهگیری ارتعاش محور و سرعت محور با پراکسیمیتر خواهیم پرداخت.
برای تعیین ارتعاش محور چرخان رو به روی آن و عمود بر محور دوران پروب پراکسیمیتی ارتعاش نصب میشود. دو حالت ممکن است پیش بیاید اگر فاصله بین پروب و محور یکسان باقی بماند، خروجی جریان گردابی نشان داده شده بر روی نمایشگر یک دامنهی ثابت را نشان میدهد که این بیانگر عدم وجود ارتعاش در محور است. حالت دوم اگر محور به علتهای مختلف از جمله خرابی بیرینگها، خوردگی، نصب نادرست و غیره دچار ارتعاش باشد فاصله بین پروب و محور به صورت مداوم تغییر میکند که وجود این مسأله سبب میشود خروجی جریان گرادابی که نمایشگر نشان میدهد به صورت مرتعش باشد که بیانگر تغییر مداوم فاصلهی بین محور و پروب است. در ضمن به محل ناهمراستایی شفت High Spot میگویند.
برای سنجش سرعت دورانی شفت، بر روی شفت یک جای شکاف یا برآمدگی ایجاد میکند تا با هر بار گردش شفت و رسیدن شکاف یا برآمدگی جلوی ترنسدیوسر کیفیزور (Keyphasor Transducer)، جریان گردابی دچار تغییر شود و با بررسی این تغییرات در طول زمان میتوان سرعت گردش محور را بدست آورد.
ابزار دقیقهای اندازهگیری جریان سیال
اندازهگیری جریان سیال، یک بخش مهم و جدایی ناپذیر از تمام فرآیندهای صنعتی است. اندازهگیری دقیق جریان سیال ورودی برای دست یافتن با کیفیت و اقتصادی مهم است. برای مثال فرض کنید برای تکمیل پخت یک محصول نیاز به تزریق بخار داغ به محفظه است اگر جریان بخار از حد مورد نیاز بیشتر باشد محصول کیفیت لازم را نخواهد داشت و اگر کمتر از مقدار مورد نیاز باشد پخت کامل نمیشود. همچنین عدم دقت در تنظیم جریان سیال سبب افزایش اتلاف انرژی خواهد شد. در ادامه با برخی از روشهای اندازهگیری جریان سیال آشنا خواهیم شد.
۱) اندازهگیری به روش اختلاف فشار
اندازهگیری به روش اختلاف فشار یا به انگلیسی Differential Pressure Flow Meter، با روشهای مختلفی مانند: اُریفیس (Orifice)، جریان نازل (Flow Nozzle) و ونتوری (Ventruri Meter) انجام میشود که پایه و اساس بر اندازهگیری افت فشار ناشی از عبور سیال از تجهیزات نام برده شده است که در ادامه برای آشنایی به بررسی ونتوری خواهیم پرداخت.
ونتوری یک روش پرکاربرد برای اندازهگیری جریان سیال است علاوه بر داشتن قابلیت اطمینان بالا، فاقد پیچیدگی است. این روش نسبت به سایر روشهای مشابه حداقل افت فشار را ایجاد میکند که از این لحاظ بسیار حائز اهمیت است. در ونتوری با استفاده از معادلات برنولی (Bernoulli’s Equation)، جریان سیال محاسبه میشود. معادله برنولی به صورت زیر است.
سیال از سطح مقطع A۱، با فشار P۱ و سرعت v۱ به داخل ونتوری با سطح مقطع A۲ هدایت میشود. از آنجایی که سطح مقطع A۲ کمتر از A۱ است باید در قسمت مقطع باریکتر سرعت سیال افزایش یابد تا بتواند همان مقدار سیال ورودی را خارج کند و بنا به قانون برنولی با افزایش سرعت سیال فشار کاهش مییابد. در لولهی ونتوری برای بررسی تغییرات فشار از دو لولهی مندرج که عمود بر جهت جریان سیال است استفاده شده است که آن را در شکل زیر مشاهده میکنید و با ثبت مقدار افت بالا آمدن سیال از لولهی مندرج (هد سیال) میتوان مقدار افت فشار را محاسبه کرد. در نهایت با دانستن سطح مقطع و فشار میتوان مقدار سرعت سیال را محاسبه کرد. رابطهی بدست آمده برای محاسبه سرعت سیال به صورت زیر است که اثبات این رابطه را میتوانید در کتب مکانیک سیالات بررسی بفرمایید.
۲) روتامتر
روتامتر یا به انگلیسی Rotameter، وسیلهایی برای سنجش جریان سیال است که توسط کارل کویپرز در سال ۱۹۰۸ میلادی ابداع شد. اساس کار این تجهیز بر اصل تعادل استاتیکی است که همزمان به شناور روتامتر دو نیروی جاذبه و درگ وارد میشود و موقعیت آن در لولهی مندرج بستگی به مقدار بر هم کنش این دو نیرو دارد.
نیروی درگ یا پسار و به انگلیسی Drag، نیروی است که به یک جسم خارجی موجود در سیال جاری وارد میشود. این نیرو همان نیروی است که وقتی دستمان را در داخل جوی آب میبریم، به دستمان وارد میشود. نیروی درگ سیال تابعی از چگالی سیال، شکل مقطع شناور و سرعت سیال است.
چگالی شناور روتامتر، از سیال مورد سنجش بیشتر است تا همواره در آن غوطه ور باشد. وقتی که سیال وارد روتامتر میشود شناور در اثر نیروی سیال به بالا هدایت میشود اما در نهایت با برهم کنش بین دو نیروی وارد شده به آن یعنی نیروی جاذبه و درگ، شناور در یک موقعیت مشخص قرار میگیرد که نشان دهندهی جریان سیال است.
از مزایای روتامتر، میتوان به ساختار سادهی آن و عدم احتیاج به نیروی محرکه اشاره کرد. همچنین این وسیله دارای محدودیتهایی مانند دقت کم و قابلیت خوانش جریان یک سیال در دمای مشخص است و اینکه ممکن است کدورت ناخالصی زیاد سیال خوانش عداد مندرج روتامتر را دشوار کند.
۳) فلومتر توربینی
فلومتر توربینی یا به انگلیسی Turbine Flow Meter، نوعی از ابزار دقیق برای سنجش جریان سیال است که به صورت مستقیم در خط لوله نصب میشود و از دو قسمت مکانیکی و الکتریکی تشکیل شده است. قسمت مکانیکی فلومتر توربینی، دارای یک پره است که با افزایش سرعت سیال، سرعت گردش آن نیز افزایش پیدا میکند. سنجش سرعت پره میتواند با روشهای مختلف انجام شود که یکی از آنها اتصال استفاده از مغناطیس است به طوری که با هر بار چرخش پره یک پالس الکتریکی ایجاد کند تا با خوانش این پالسها با تجهیز الکتریکی بکار رفته در فلومتر توربینی، جریان سیال معادل بدست آید.
به این مقاله چقدر امتیاز میدهید؟
Rating 3.87 from 45 votes
این صفحه را با دیگران به اشتراک بگذارید و امتیاز بگیرید
برای نوشتن دیدگاه باید وارد بشوید.