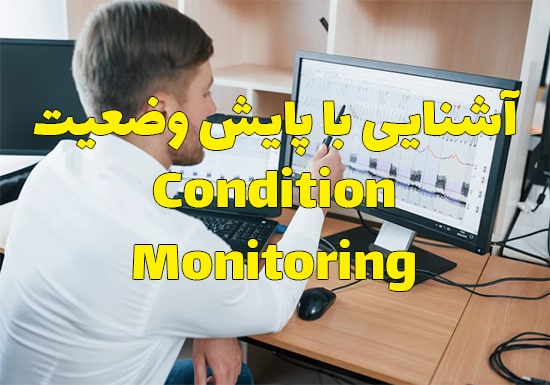
۰ تا ۱۰۰ آشنایی با پایش وضعیت Condition Monitoring
امروزه با پیشرفت علم و تکنولوژی، تلاش میشود با مراقبتهای دقیق که به طور همیشگی از دستگاهها و ماشین آلات انجام میشود بهترین شرایط عملیاتی را برای آنها فراهم آورد. به منظور نیل به این هدف، شرایط کاری ماشین به دقت زیر نظر گرفته میشود تا بتوان عیب دستگاه را قبل از آنکه وارد مرحله بحرانی شود؛ در نطفه شناسایی و خفه کرد.
از آنجایی که هزینههای نگهداری و تعمیرات همواره وجود دارد، تلاشهای زیادی برای کاهش این هزینهها شده است. نتیجه این تلاشها منجر به ایجاد و بکارگیری روشهایی شده است که با کاهش این هزینهها ابقای صنعت را در بازار رقابتی امروز تثبیت کند. در روشهای نوین به این دانش رسیدهاند که با تمرکز بیشتر بر روی نگهداری میتوان هزینهها را کاهش داد. همانطور که پیشگیری بهتر از درمان است باید تلاش بر این باشد که نگهداری بهتر از تعمیرات است؛ به این فرهنگ عمومی تبدیل شود.
استفاده از روشهای مؤثر نگهداری و تعمیرات (نت) نه تنها سبب افزایش سودآوری شرکت خواهد شد بلکه ابقای صنعت را در بازار رقابتی امروز را تضمین میکند. در مقاله ۰ تا ۱۰۰ آشنایی با انواع روشهای نگهداری و تعمیرات به بررسی انواع روشهای نگهداری و تعمیرات پرداخته شد. یکی از سیاستهایی که برای نت دنبال میشود نت بر اساس شرایط کار یا پایش وضعیت (Condition Monitoring) است.
سیاست پایش وضعیت میتواند در نت اصلاحی یا پیشگیرانه یا پیش بینانه مورد استفاده قرار گیرد. اما استفاده از این سیاست با توجه به فلسفه بنیادی آن که ما آن را استفاده میکنیم تا از شرایط دستگاه با خبر باشیم و از بروز خرابی غیر منتظره یا تعویض غیر ضروری جلوگیری کنیم؛ بیشتر با نت پیش بینانه همراه است.
اهمیت استفاده از پایش وضعیت Condition Monitoring
در مقاله پیشین ۰ تا ۱۰۰ آشنایی با انواع روشهای نگهداری و تعمیرات، به بررسی محدودیتهای هر کدام از روشهای نت پرداخته شد. مشخص شد که در صنایع مهم و بزرگ چنانچه از نت اصلاحی استفاده شود بروز خرابیهای غیر منتظره، سبب تحمیل هزینههای سنگین به مجموعه میشود. از طرف دیگر دنبال کردن سیاست نت پیشگیرانه با پیش فرض اینکه هر قطعه عمر محدودی دارد و باید قبل از پایان عمر، آن را تعویض کرد سبب تحمیل هزینه زیاد خواهد شد. گرچه نت پیشگیرانه در صنایع هوایی توصیه شده است و بسیاری از تولیدکنندگان به علت افزایش درآمد ناشی از فروش بیشتر قطعات یدکی این روش را پیشنهاد میکنند اما استفاده کردن از این الگو در صنایع بزرگ توجیه اقتصادی ندارد.
پس در صنایع بزرگ به این نتیجه رسیدهاند که؛ تحت نظر قرار دادن عملکرد دستگاه، میتواند از خرابی غیر منتظره جلوگیری کند و همچنین از حداکثر عمر مفید تجهیز بهره برد. در نتیجه تکنیکهای پایش وضعیت در الگوی نت پیش بینانه بکار گرفته شد تا بتوان از تجهیزات حیاتی خط تولید به شکل مؤثر استفاده کرد.
اصول کار Condition Monitoring
هر سیستم الکتریکی، مکانیکی، هیدرولیکی، دینامیکی یا حرارتی در هنگام کار دارای یک سری مشخصات و علائم خاص میباشد که بروز یک سری تغییرات در علائم و نشانهها نماینگر ظهور عیب است. در تکنیک Condition Monitoring با دریافت و تحلیل این اطلاعات قادر خواهیم بود خرابی سیستم را پیشبینی کنیم.
اهداف و مزایای پایش وضعیت
۱) به حداقل رساندن تعداد دفعات توقف خط تولید
استفاده از تکنیک پایش وضعیت سبب خواهد شد که از وضعیت ماشین اطلاعات کامل در اختیار داشته باشیم. در نتیجه از بروز خرابیهای غیر منتظره که نتیجه آن توقف طولانی مدت خط تولید است، جلوگیری شود.
۲) کاهش زمان انجام تعمیرات
اگر پایش دقیقی از وضعیت دستگاه داشته باشیم قادر خواهیم بود عیب آن را به درستی تشخیص بدهیم. در نتیجه برای انجام تعمیرات از قبل با گردآوری افراد متخصص و قطعات یدکی لازم زمان انجام تعمیرات را به حداقل میرسانیم.
۳) کاهش مصرف قطعات یدکی
با استفاده از تکنیک پایش وضعیت قادر خواهیم بود تعویض قطعات معیوب را زمانی انجام دهیم که حداکثر عمر مفید خود را کرده باشند. در نتیجه از تعویض غیر ضروری قطعات اجتناب میشود.
۴) افزایش کیفیت محصول
ادامه کار ماشین با وجود نقیصه در بسیاری از موارد میتواند سبب افت کیفیت محصول شود. با استفاده از تکنیک پایش وضعیت تغییرات کوچک در وضعیت ماشین قابل رهگیری است در نتیجه میتوان عیوب احتمالی را سریع برطرف کرد.
اجزای تکنیک Condition Monitoring
۱) سختافزار: سختافزار شامل انواع ابزار دقیق، سنسور، ترانسدیوسر و در مجموع کلیه تجهیزات و ابزار آلاتی است که برای اندازهگیری، ثبت و نگهداری علائم کارکرد ماشین مورد استفاده قرار میگیرد.
۲) نرمافزار: نرمافزار رابطی است که روی اطلاعات دریافت شده از سختافزار پردازشهای گوناگون انجام میدهد و این اطلاعات را برای تفسیر آماده میکند.
۳) کارشناس پایش وضعیت (CM): نیروی کارشناس پایش وضعیت علاوه بر مدیریت بکارگیری سختافزار و نرمافزار، وظیفه تحلیل دادههای جمعآوری شده را نیز بر عهده دارد. وی با پشتوانه تجربیات پیشین سعی در ریشهیابی عیب موجود در سیستم با استفاده از دادههای دریافت شده را دارد. امروزه با توسعهی نرم افزاری و ابزار آلات جدید مانند ماشین لرنینگ، هوش مصنوعی و… اتکا به نقش نیروی انسانی کمرنگتر شده است اما استفاده از کارشناس امری اجتناب ناپذیر است.
لازم به ذکر است که برای اجرای موفقیتآمیز تکنیک Condition Monitoring و دستیابی به نتایج مؤثر بکارگیری صحیح از هر سه ابزار فوق ضروری میباشد.
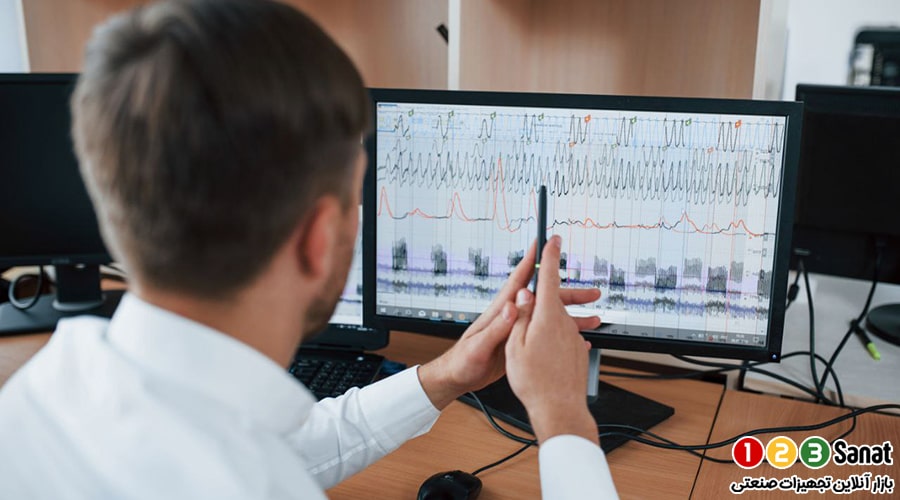
تکنیکهای پایش وضعیت
تجهیزات مختلف با توجه به مکانیزم کاریشان علائم مشخصه متفاوتی را دارند. برای شناسایی این علائم تکنیکهای مختلفی توسعه پیدا کردهاند. تکنیکهای مختلف بر روی سنجش پارامترهای و مشخصههای مختلف یک تجهیز تمرکر دارند. این تکنیکها شامل: آنالیز ارتعاشات، آنالیز روغن، آنالیز دما و… میباشد.
هر کدام از تکنیکهای فوق کاربرد مشخصی دارند و برای پایش وضعیت یک ماشین مناسبتر میباشند. البته که در برخی از ماشینها به واسطه نوع کارشان میتوان از چند تکنیک مختلف برای پایش وضعیت استفاده کرد. در جدول زیر کاربرد روشهای مختلف پایش وضعیت نشان داده شده است.
تکنیک | تجهیزات | کاربرد |
---|---|---|
ترموگرافی | پیرومتر (Pyrometer)، دوربین مادون قرمز | یاتاقانها، تجهیزات برقی، نشت سیال، عایقهای حرارتی و … |
آنالیز صوت | میکروفن، صدا سنج | صدای موتور، نشت سیال تحت فشار، رینگ پیستون |
آنالیز ارتعاشات | آنالیز، شتاب سنج | یاتاقانها، گیربکس، عدم هم محوری، نامیزانی، خمیدگی و سائیدگی شافتها، بررسی ترک و عدم روانکاری صحیح |
تست غیر مخرب NDT | تست التراسونیک، تست جریان گردابی، تست رادیوگرافی و … | بررسی تغییر ضخامت، وجود ترک و وجود خوردگی |
آنالیز روغن | تجهیزات آنالیز روغن | ارزیابی وضعیت روغن و وجود ذرات سائیده شده در روغن |
تجزیه و تحلیل جریان الکتریکی | تجهیزات مربوطه | ارزیابی کارکرد موتورهای الکتریکی و ژنراتورها |
تجزیه و تحلیل عملکرد | تجهیزات مربوطه | توربین، موتور، کمپرسور، پمپ |
۱) تکنیک آنالیز ارتعاشات
ارتعاشات جزء جدایی ناپذیر تمام مکانیزمهای انتقال نیرو میباشد. مقدار این ارتعاش در ماشینهای مختلف با توجه به نحوهی کارشان متفاوت است. مقدار ارتعاش معمولاً با عمر ماشین رابطه مستقیم دارد و هر چه عمر ماشین بیشتر میشود با فرسایش و سائیدگی قسمتهای مختلف لقی آن افزایش مییابد؛ در نتیجه ارتعاشات ایجاد شده بیشتر میشود.
افزایش مقدار ارتعاشات اگر بیشتر از مقدار مجاز تعریف شده باشد نه تنها سبب اتلاف انرژی در سیستم میشود بلکه استهلاک ماشین را تسریع میبخشد.
هر حرکت که دارای ارتعاش باشد با سه مشخصهی دامنه، فرکانس و فاز مشخص میشود. دامنه ارتعاشات بزرگی مقدار ارتعاش را نشان میدهد. هر چه بزرگی ارتعاشات بیشتر باشد؛ شدت عیب ماشین بیشتر است. فرکانس و فاز ارتعاشات هم بستگی به نوع ارتعاش دارد.
در تکنیک آنالیز ارتعاشات، میزان ارتعاشات با استفاده از سنسورهای مخصوص اندازهگیری میشود. برای این منظور پارامترهای جابجایی، سرعت و شتاب ارتعاشات اندازهگیری میشود. تصمیمگیری در خصوص انتخاب نوع یا نوعهای پارامتر اندازهگیری، بستگی به اهداف اندازهگیری و شرایط کاری ماشین دارد.
عمده مشکلات مکانیکی ماشین آلات دوار به صورت علائم ارتعاشی یا تغییر در مشخصههای ارتعاشی سیستم ظاهر میشوند در نتیجه میتوان با تحلیل ارتعاش، به عیب موجود در سیستم پی برد. عمده عیوبی که با آنالیز ارتعاشات قابل شناسایی هستند شامل: عدم هم محوری (Misalignment)، خمیدگی شافت، خروج از مرکز، لقی مکانیکی، مشکلات یاتاقانهای ژورنال، مشکلات بیرینگهای غلتشی، کاویتاسیون و مشکلات گیربکس (جعبه دنده) میباشند.
۲) تکنیک آنالیز روغن
آنالیز روغن یکی دیگر از تکنیکهای پایش وضعیت است. وظیفه اصلی روغن روانکاری میباشد. در صورتی که روغن خاصیت خود را از دست بدهد، دو سطح رو هم سائیده میشوند و مقدار سایش به شدت افزایش مییابد. روغن در بسیاری از سیستمهای صنعتی نقش اصلی را دارد. در یاتاقانهای ژورنال هیدرودینامیک روغن وظیفه ایجاد لایه نازک روانکار برای کار تجهیز را دارد. در سیستمهای هیدرولیکی انتقال قدرت به وسیله روغن انجام میشود. در نتیجه واضح است که توجه به سلامت روغن برای جلوگیری از تخریب ماشین ضروری میباشد.
روغنها که در ماشینها مورد استفاده قرار میگیرند پس از مدتی ناخالصیهایی مانند: ذرات سائیده شده، گرد و غبار، آب، دوده واردشان میشوند و روغن به مرور خاصی خود را از دست میدهد. با آنالیز روغن میتوان از وجود هر گونه آلایندگی در روغن اطلاع پیدا کرد و از سلامت روغن مطمئن شد. علاوه بر موارد ذکر شده آنالیز روغن قابلیت تشخیص تغییر در ویسکوزیته روغن را دارد. اگر ویسکوزیته روغن کاهش یابد، قادر به تشکیل حداقل ضخامت فیلم روانکار نحواهد بود در نتیجه سایش به وجود میآید. از طرف دیگر اگر ویسکوزیته روغن افزایش یابد روغن قابلیت روانکاری مجاری باریک را به علت عدم نفوذ روغن از دست خواهد داد.
آنالیز روغن امکان ریشهیابی عیب را نیز فراهم میکند. برای مثال با سنجش میزان اسیدی یا بازی بودن روغن نوع آلودگی وارد شده به روغن شامل آب، دوده، خاک و سوخت مشخص میشود. علاوه بر این اندازهگیری ذرات سایشی در آنالیز روغن با روشهای طیفنگاری جذب اتمی (AAS)، طیفنگاری نشر اتمی (AES) و طیفنگاری اشعه ایکس (XRF) این امکان را فراهم میکند با توجه به جنس سایز ذره سائیده شده قطعه معیوب که دچار سایش شده است را شناسایی کرد.
۳) تکنیک آنالیز دما
آنالیز دما یکی دیگر از تکنیکهای پایش وضعیت است که با ارزیابی مشخصهی دما متوجه وجود عیب در داخل تجهیز میشویم. بسیاری از عیوب مانند بالارفتن اصطکاک، از کار افتادن سیستم خنک کاری، عیب برقی و… سبب بالارفتن دما در تجهیز میشوند.
آنالیز دما به دو صورت امکانپذیر است. در حالت اول دمای قطعه به وسیله یک دما سنج اندازهگیری میشود و اگر دما از حد مجاز بالاتر رفت؛ کاربر با دریافت یک آلارم از وجود دمای بالا مطلع میگردد. این روش با نام سیستم پایش دما شناخته میشود. این سیستم در عمده تجهیزات برقی اعم از رایانه، خودرو و… وجود دارد. در حالت دوم با استفاده از دوربینهای ترموگرافی از قطعه و اجزای مورد نظر عکس حرارتی گرفته میشود. اصول کار این تکنیک به این صورت است که کلیه سطوح بسته به میزان درجه حرارتشان داری نرخ تششع حرارتی هستند و تفاوت در درجه حرارت سبب ایجاد تفاوت در میزان تابش امواج مادون قرمز خواهد شد. دوربین ترموگرافی قابلیت ظاهر کردن این امواج مادون قرمز که برای چشم ما نامرئی است را دارد.
مزیت اصلی روش آنالیز دما، غیر تماسی بودن آن است. در نتیجه میتوان از فاصله مناسب از تجهیز عکسبرداری کرد و با دریافت اطلاعات لازم، نسبت به تحلیل دادهها اقدام کرد.
۴) تکنیک آنالیز صدا
تکنیک آنالیز صدا یک روش تشخیص و رفع عیوب در تجهیزات صنعتی است که بر اساس تحلیل و شناخت الگوهای صداهای تولید شده توسط تجهیزات صورت میگیرد. از طریق بررسی الگوهای صوتی تولید شده توسط تجهیزات و بررسی تغییرات الگوی صدا میتوان به وضعیت غیر عادی کار کردن تجهیز پی برد.
برای انجام آنالیز صدا، ابتدا صداهای تجهیزات در شرایط عادی ضبط میشوند. سپس در زمان عملکرد نامطلوب یا بروز عیب، صداهای مرتبط دوباره ضبط میشوند. با مقایسه الگوهای صوتی در دو حالت، ممکن است الگوهای خاصی که به تغییرات ناشی از عیب اشاره دارند، شناسایی شوند.
این تکنیک میتواند در پیشگیری از خرابیهای غیرمنتظره، کاهش هزینههای تعمیر و نگهداری و افزایش بهرهوری کاربرد داشته باشد. برخی از عیوب مربوط به یاتاقانها، گیربکسها (جعبه دندهها)، پمپها و کمپرسورها و هم چنین کاویتاسیون را میتوان با تکنیک آنالیز صدا تشخیص داد.
در تکنیک آنالیز صدا، از الگوریتمهای پردازش سیگنال مانند FFT (تبدیل فوریه سریع) برای تحلیل طیف صوتی و الگوهای فرکانسی استفاده میشود. همچنین، تکنیکهای پیشرفتهتر مثل ماشین یادگیری میتوانند در تشخیص و تحلیل دقیقتر الگوهای صوتی و تفاوتهای ناشی از عیب کمک کنند.
نکتهایی که توضیح آن مفید میتواند باشد آنالیز ارتعاشات معمولاً در محدودهی فرکانسی ۱ تا ۲۰ کیلو هرتز بررسی انجام میشود در حالی که در آنالیز صدا محدودهی فرکانسی معمولاً بین ۲۰ تا ۱۰۰ کیلو هرتز میباشد. علاوه بر این از دیدگاه حسگرها و نوع اطلاعات مورد بررسی، تفاوتهای معنیداری بین این دو وجود دارد.
۵) تکنیک تجزیه و تحلیل عملکرد
تکنیک تجزیه و تحلیل عملکرد یا Performance Analysis به بررسی و ارزیابی عملکرد و کارایی تجهیزات میپردازد. این تکنیک از آنجایی بسیار مهم است که یک تجهیز در ظاهر ممکن است بدون مشکل در حال کار باشد اما بازدهی آن کاهش یافته باشد اما این کاهش بازده با سایر روشهای پایش وضعیت مانند آنالیز ارتعاشات، آنالیز دما و غیره قابل تشخیص نباشد. در نتیجه این تغییر در بازدهی، اگر سریعاً بررسی و رفع نگردد سبب کاهش افت کیفیت محصول و کاهش سودآوری شرکت خواهد شد.
این تکنیک به منظور بهبود فرآیندها، افزایش بهرهوری، کاهش هزینهها و جلوگیری از خرابیهای ناگهانی مورد استفاده قرار میگیرد.
برخی جنبههای مهم تکنیک تجزیه و تحلیل عملکرد در تجهیزات صنعتی عبارتند از:
۱)مانیتورینگ و ثبت داده: دادههای مربوط به عملکرد تجهیزات از طریق سنسورها، دستگاههای اندازهگیری و سیستمهایمانیتورینگ جمعآوری میشود.
۲) تحلیل داده: از تکنیکهای تجزیه و تحلیل داده برای درک الگوها، شناسایی علل مشکلات و بهبود نقاط ضعف در عملکرد استفاده میشود.
۳) پیشبینی و پیشگیری از خرابی: استفاده از مدلهای پیشبینی بر اساس دادههای جمعآوری شده به منظور تشخیص مشکلات قبل از اینکه به ابعاد جدی تبدیل شوند.
۴) بهبود کارایی: فرصتها برای بهبود عملکرد و افزایش بهرهوری تجهیزات شناسایی میشود.
۵) بهینهسازی فرآیندها: فرآیندها و شناسایی مسیرهای بهینه برای اجرای وظایف ارزیابی میشود.
۶) پیشنهاد تعمیرات پیشگیرانه: زمان مناسب برای تعمیرات و نگهداری پیشگیرانه بر اساس دادههای عملکرد تعیین میشود.
با استفاده از تکنیک تجزیه و تحلیل عملکرد، کارشناسان میتوانند به نحو اثربخشی فعالیتها و تجهیزات را مدیریت کنند و از عیوب و نقاط ضعف جلوگیری کنند.
۶) تجزیه و تحلیل جریان الکتریکی
تجزیه و تحلیل جریان الکتریکی یا Motor Current Signature Analysis (MCSA) یک تکنیک پیشرفته در زمینه تشخیص مشکلات و ارزیابی عملکرد موتورها است. این تکنیک بر اساس تحلیل الگوی جریان الکتریکی موتورها در طول زمان صورت میگیرد.
با توجه به اهمیت ماشینهای الکتریکی (موتورهای الکتریکی، ژنراتورها) در صنعت، نگهداری تعمیرات آنها از اهمیت بسیار بالایی برخوردار است. تکنیک تجزیه و تحلیل جریان الکتریکی در کنار سایر روشهای پایش وضعیت مانند آنالیز ارتعاشات و آنالیز دما کارکرد صحیح تجهیز را اطلاع میدهد. با استفاده از این تکنیک عیوبی مانند: شکست میلههای روتور، خروج از مرکز، خرابی یاتاقانها و نامیزانی قابل تشخیص میباشد.
روش کار این تکنیک به این صورت است که سیگنال جریان ماشینهای الکتریکی در وضعیتایدهآل به صورت یک موج سینوسی ساده است که در طیف آن یک فرکانس قابل مشاهده است. بروز هر گونه عیب در ماشین الکتریکی سبب تغییر در شار مغناطیسی در حین کارکرد دستگاه خواهد شد. از آنجایی که هر عیب با یک تغییر در شار متناظر است با تحلیل این تغییرات میتوان به عیوب پیدا شده در ماشین پی برد.
به این مقاله چقدر امتیاز میدهید؟
Rating 4.57 from 7 votes
این صفحه را با دیگران به اشتراک بگذارید و امتیاز بگیرید
برای نوشتن دیدگاه باید وارد بشوید.