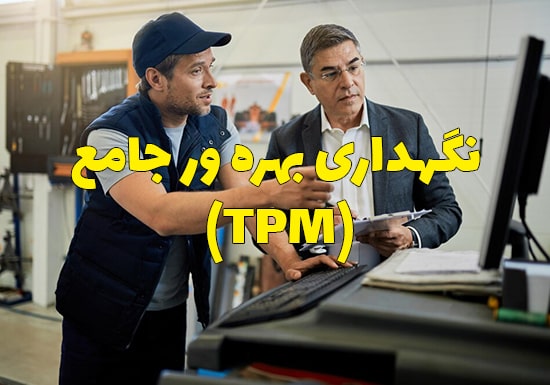
۰ تا ۱۰۰ آشنایی با نگهداری بهره ور جامع TPM
در مقاله ۰ تا ۱۰۰ آشنایی با انواع روشهای نگهداری و تعمیرات، به بررسی انواع روشهای نگهداری و تعمیرات پرداخته شده است. در مقاله نامبرده اشاره شد که یکی از روشهای نوپا در دانش نگهداری و تعمیرات (نت)، روش نگهداری بهره ور جامع TPM که مخفف عبارت Total Productive Maintenance است، میباشد.
نگهداری بهره ور جامع (TPM) فرآیند استفاده از ماشین آلات، تجهیزات، کارکنان و فرآیندهای پشتیبانی برای حفظ و بهبود یکپارچگی تولید و کیفیت سیستمها است.
برای درک مفهوم TPM باید در ابتدا با کلمه Productive به معنای بهره وری آشنا شد. بهره وری از مفاهیم علم اقتصاد و مدیریت است که چنین تعریف میشود: بهدست آوردن حداکثر سودِ ممکن با بهره گیری و استفاده بهینه از نیروی کار، استعداد، زمین، ماشین، پول، تجهیزات، زمان، مکان، مهارت نیروی انسانی و … به منظور ارتقای رفاه جامعه. به عبارت دیگر بهره وری بیان میکند کارایی باید همراه با اثر بخشی باشد.
هدف از نگهداری بهره ور جامع، این است که علم نگهداری با بهره وری توام کرد. تعاریف مختلفی برای نگهداری بهره ور جامع وجود دارد. یکی از تعریفهای کامل از TPM به صورت زیر است.
«نگهداری بهره ور جامع یک فرآیند بهبود سازمان یافته متمرکز است که سعی دارد بهره وری تمامی تجهیزات را از طریق مشارکت تمامی پرسنل در کل سطوح مجموعه در قالب تیمهای مشارکتی بهینه نماید.»
اهمیت اجرای نگهداری بهره ور جامع TPM
بعد از بحران اول نفت در سال ۱۹۷۳ میلادی (۱۳۵۱ شمسی) و بحران دوم نفت در سال ۱۹۷۸ میلادی (۱۳۵۶ شمسی)، بسیاری از کمپانیهای غربی متوجه عقب افتادگی خود در مقابل کمپانیهای ژاپنی شدند. آنها سعی کردند با الگوبرداری از روشهای استفاده شده توسط کمپانیهای ژاپنی این عقب افتادگی را جبران کنند. این تلاشها آنها را واداشت که در جهت پیادهسازی تولید ناب (Lean Production) اقدام کنند. تولید ناب یعنی حذف ضایعات از فرآیند تولید. این مهم در صورت اجرای صحیح TPM امکانپذیر است.
اجرای نگهداری بهره ور جامع، نشان داده است که کاهش ضایعات، افزایش زمان عملیاتی تجهیزات، حداقل کردن اتلاف زمان، تقلیل حوادث، افزایش بهره وری، افزایش مشارکت کارکنان و اجرای کار با نیروی کار کمتر همگی از نتایج موفقیتآمیز این روش بوده است.
اجرای صحیح TPM به سادگی امکانپذیر نیست؛ کما ینکه آمارهای گوناگون نشان میدهد که به صورت تقریبی بین ۶۰ تا ۹۰ درصد تلاشها برای پیادهسازی این روش با شکست همراه میشود. اندازهگیری اثر بخشی TPM با شاخص فرآیند کلیدی (KPI) ممکن است. این شاخص، نتیجه را به PQCDSM معطوف میداند. PQCDSM در برگیرنده ۶ مفهوم به به این شرح است. Production (بهره وری)، Quality (کیفیت)، Cost (هزینه)، Delivery (تحویل)، ایمنی (Safety) و Morale (روحیه).
سوزوکی (Suzuki)، بیان میکند در اولین اجرای TPM در ژاپن نتایج زیر بدست آمده است.
P – Productivity (بهره وری):
بهره وری ۱/۵ تا ۲ بار افزایش یافت.
از کار افتادگی تجهیزات ۱/۱۰ تا ۱/۲۵۰ کاهش یافت.
بهره وری کلی کارخانه ۱/۵ تا ۲ برابر افزایش یافت.
Q – Quality (کیفیت)
نرخ ضایعات فرآیند تا ۹۰ درصد کاهش یافت.
نارضایتی مشتری و کالای مرجوعی تا ۷۵٪ کاهش یافت.
C – Cost (هزینهها)
هزینههای تولید تا ۳۰٪ کاهش یافت.
D – Delivery (تحویل)
قطعات آماده تحویل و قطعات در جریان کار ۵۰٪ کاهش یافت.
S – Safety (ایمنی)
توقفهای ناگهانی از بین رفت.
وقایع آلاینده از بین رفت.
M – Morale (روحیه)
پیشنهادات در جهت بهبود توسط پرسنل ۵ تا ۱۰ برابر افزایش یافت.
۸ رکن نگهداری بهره ور جامع (TPM)
نگهداری بهره ور جامع توسط سویچی ناکیجیما (Seiichi Nakajima) در ژاپن توسعه داده شد. نتایج کار او روی این موضوع منجر به ابداع روش TPM در اواخر دهه ۱۹۶۰ و اوایل دهه ۱۹۷۰ شد. TPM، با ترکیب تکنیکهای تولید ناب (lean manufacturing)، بر روی هشت ستون بر اساس سیستم ۵S ساخته شده است. سیستم ۵S یک روش سازمانی است که بر پایه پنج کلمه ژاپنی که معنای آن در ادامه آمده است، بنا شده است:
۱) Seiri (سازماندهی): بهم ریختگی از فضای کاری حذف کنید.
۲) Seiton (نظم): با پیروی از “مکانی برای همه چیز و هر چیزی در جای خود” نظم را تضمین کنید.
۳) Seiso (تمیز بودن): فضای کار را تمیز کنید و آن را به همین صورت نگه دارید.
۴) Seiketsu (استاندارد کردن): همه فرآیندهای کاری را استاندارد کرده و آنها را سازگار میکند.
۵) Seiketsu (حفظ): به طور مداوم چهار مرحله اول را تقویت میکند.
هشت رکن نگهداری بهره ور جامع بر تکنیکهای پیشگیرانه (preventive) و پیشگویانه (proactive) برای کمک به بهبود قابلیت اطمینان تجهیزات تمرکز دارند. هشت رکن عبارتند از: ۱) بهبود متمرکز (Focused Improvement) ۲) نگهداری خود گردان (Autonomous Maintenance) ۳) نگهداری برنامهریزی شده (Planned Maintenance) ۴) آموزش (Training Maintenance) ۵) مدیریت اولیه تجهیزات (Early Equipment Management) ۶) نگهداری کیفی (Quality Maintenance) ۷) ایمنی، سلامت و محیط (Safety، Health & Environment) ۸) نگهداری بهره ور جامع ستادی (TPM in Administration).
۱) بهبود متمرکز (Focused Improvement)
بهبود متمرکز بر اساس اصطلاح ژاپنی “کایزن (Kaizen)” میباشد. کایزن، به معنای بهبود یا تغییر مستمر برای رسیدن به نتیجهای بهتر میباشد.
بهبود متمرکز به فرآیند به عنوان یک کل نگاه میکند و ایدههایی را برای چگونگی بهبود آن ایجاد میکند. برای انجام بهبود متمرکز در TPM، قرار دادن تیمهای کوچک با ذهنیت کار فعالانه با هم برای اجرای اصلاحات منظم و تدریجی در فرآیندهای مربوط ضروری میباشد. هماندیشی اعضای مختلف تیم امکان شناسایی مشکلات تکرار شونده را از طریق ارائه نظرات مختلف فراهم میکنند.
علاوه بر این، بهبود متمرکز با کاهش عیوب محصول و تعداد فرآیندها، با تجزیه و تحلیل خطرات هر اقدام فردی، ایمنی و کارایی را افزایش میدهد. در نهایت، بهبود متمرکز تضمین میکند که بهبودها استاندارد شدهاند و آنها را تکرارپذیر و پایدار میسازد.
۲) نگهداری خود گردان (Autonomous Maintenance)
نگهداری خود گردان به این معنی است که اطمینان حاصل شود اپراتور تجهیزات مربوطه به طور کامل آموزش دیدهاند و با داشتن احساس مالکیت بر تجهیزات خود نگهداری و تعمیرات در زمینه معمول مانند تمیز کردن، روغن کاری و بازرسی را انجام میدهند. این موضوع به شناسایی مشکلات قبل از خرابی کمک خواهد کرد و کارکنان نگهداری و تعمیرات را برای کارهای سطح بالاتر آزاد میکند.
اجرای نگهداری خود گردان، بر اساس نوع کارکرد ماشین تدوین میشود و استانداردسازی این فرآیند تضمین میکند که همه فرآیندها از رویهی یکسانی پیروی میکنند.
۳) نگهداری برنامهریزی شده (Planned Maintenance)
نگهداری برنامهریزی شده شامل مطالعه معیارهایی مانند: نرخ خرابی و تاریخ خرابیها و سپس برنامهریزی نگهداری و تعمیرات بر اساس آنها میباشد. به عبارت دیگر، این مطالعه برای برنامهریزی نگهداری و تعمیرات در زمانی که تجهیزات در Shut Down هستند یا با ظرفیت کم در حال کار هستند، انجام میشود. علاوه بر این، نگهداری برنامهریزی شده امکان جمعآوری امکانات و وسایل را برای زمانی که تعمیرات برنامهریزی شده است را فراهم میکند.
اتخاذ این رویکرد میزان خرابیهای برنامهریزی نشده را تا حد زیادی کاهش میدهد، زیرا اجازه میدهد بیشتر تعمیرات در زمانهایی که ماشین آلات برای تولید برنامهریزی نشدهاند، برنامهریزی شود. همچنین به شما این امکان را میدهد که با کنترل بهتر موجودی قطعاتی که مستعد فرسودگی و خرابی هستند، را با دقت بیشتری برنامهریزی کنید.
۴) آموزش (Training Maintenance)
فقدان دانش در مورد تجهیزات میتواند برنامه TPM را از مسیر خارج کند. آموزش برای اپراتورها، و پرسنل نگهداری و تعمیرات و مدیران اعمال میشود تا همه با فرآیند TPM آشنا شوند. در این آموزشها پرسنل میآموزد که چگونه یک برنامه نگهداری و تعمیرات پیشگیرانه (preventive) و پیشگویانه (proactive) با اتکا به اصول TPM اجرا کنند.
۵) مدیریت اولیه تجهیزات (Early Equipment Management)
رکن مدیریت اولیه تجهیزات در TPM، یعنی از دانش و تجربه عملی برای بهبود طراحی تجهیزات جدید استفاده شود. طراحی تجهیزات با مشارکت افرادی که بیشتر از آن استفاده میکنند به تأمینکنندگان اجازه میدهد تا قابلیت نگهداری و نحوه عملکرد دستگاه را در طراحیهای آینده بهبود بخشند.
هنگام بحث در مورد طراحی تجهیزات، مهم است که در مورد مواردی مانند سهولت تمیز کردن و روغن کاری، دسترسی به قطعات، قرار دادن ارگونومیک کنترلها به گونهای که برای اپراتور راحت باشد، نحوه تغییر و ویژگیهای ایمنی صحبت کنید. اتخاذ این رویکرد، کارایی را افزایش میدهد زیرا تجهیزات جدید از قبل مشخصات مورد نظر را برآورده میکنند و مشکلات راهاندازی کمتری دارند، بنابراین سریعتر به سطوح عملکرد برنامهریزی شده میرسند.
۶) نگهداری کیفی (Quality Maintenance)
تمام برنامهریزیها و استراتژیهای نگهداری و تعمیرات، اگر نگهداری کیفی در آن انجام نشود، بیهوده است. رکن نگهداری کیفی بر تشخیص خطای طراحی و جلوگیری از ورود آن به فرآیند تولید تمرکز دارد. این کار را با استفاده از تجزیه و تحلیل علت ریشهای انجام میشود. یکی از تکنیکهای مؤثر برای حذف منابع تکرار شونده نقص، تکنیک «۵ چرا (۵ Whys)» است.
تکنیک ۵ چرا یک روش سؤال پرسی برای برای پی بردن به روابط علت و معلولی در مورد یک مسأله یا مشکل خاص است. هدف اصلی این روش، یافتن علت اصلی وقوع یک نقص یا مشکل است. این تکنیک توسط ساکیشی تویودا (مؤسس تویوتا)، ابداع شد. نحوه استفاده از این تکنیک به این صورت است که مثلاً برای یافتن علت روشن نشدن خودرو، ۵ دلیل ارائه میشود و تلاش میشود برای مشکل یک راهکار پیدا شود.
با شناسایی فعالانه منبع خطا یا نقص، فرآیندها قابل اعتمادتر میشوند و محصولاتی با مشخصات مناسب تولید میکنند. در نتیجه با نگهداری کیفی، مسائل مربوط به کیفیت برطرف میشود و اقدامات متقابل دائمی انجام میشود که نقصها و خرابیهای مربوط به محصولات معیوب را به حداقل رسانده یا کاملاً از بین میبرد.
۷) ایمنی، سلامت و محیط زیست (Safety، Health & Environment)
حفظ محیط کار ایمن به این معنی است که کارکنان میتوانند وظایف خود را در مکانی امن و بدون خطرات بهداشتی انجام دهند. ایجاد محیطی که تولید را کارآمدتر میکند بسیار مهم است، اما نباید ایمنی و سلامت کارمندان را به خطر بیندازد. برای دستیابی به این هدف، هر راه حلی که در فرآیند TPM معرفی میشود باید همیشه ایمنی، سلامت و محیط زیست را در نظر بگیرد.
جدای از مزایای آشکار، هنگامی که کارکنان هر روز در محیطی امن به محل کار میآیند، نگرش آنها بهتر میشود، زیرا آنها نیازی به نگرانی در مورد این جنبه مهم ندارند. این میتواند بهره وری را به طور قابل توجهی افزایش دهد.
۸) TPM ستادی (TPM in Administration)
یک برنامه TPM خوب فقط به اندازه مجموع قطعات آن خوب است. در TPM ستادی، کل فرآیندهای کارخانه تحت نظر قرار میگیرد و ضایعات در عملکردهای آن حذف میشود.
به عنوان مثال عملکردهای اداری اغلب اولین گام در کل فرآیند تولید هستند، بنابراین مهم است که آنها ساده و بدون ضایعات باشند. به عنوان مثال، اگر روشهای پردازش سفارش سادهتر شوند، مواد سریعتر و با خطاهای کمتری به خط تولید کارخانه میرسند و زمان از اتلاف شده احتمالی را از بین میبرد.
نحوه استقرار TPM در سازمان
استقرار نگهداری بهره ور جامع (TPM) در سازمان در در نظر گرفتن انجام ۵ مرحله اصلی زیر میباشد.
۱) تعیین یک منطقه آزمایشی (identifying a pilot area)
۲) بازگرداندن تجهیزات به شرایط عملیاتی اولیه (restoring equipment to prime operating condition)
۳) اندازهگیری بهره وری کلی تجهیزات OEE (measuring OEE)
۴) رسیدگی و کاهش تلفات عمده (addressing and reducing major losses)
۵) اجرای نگهداری و تعمیرات برنامهریزی شده (implementing planned maintenance)
۱) تعیین یک منطقه آزمایشی
تعیین یک منطقه آزمایشی (identifying a pilot area) برای شروع پیادهسازی به جلب پذیرش بیشتر کارکنان با دیدن مزایایی که از این فرآیند حاصل میشود کمک میکند. با انتخاب یک منطقه آزمایشی میتوان نقاط ضعف سیستم را در اجرای کامل TPM شناسایی کرد و بهبود داد.
۲) بازگرداندن تجهیزات به شرایط عملیاتی اولیه
بازگرداندن تجهیزات به شرایط عملیاتی اولیه (restoring equipment to prime operating condition)، حول سیستم 5S و نگهداری خود گردان (Autonomous Maintenance) میچرخد. اول، شرکتکنندگان TPM باید یاد بگیرند که به طور مداوم تجهیزات را با استفاده از سیستم 5S در شرایط اولیه خود نگه دارند. این مهم شامل سازماندهی (organize)، تمیزی (cleanliness)، نظم (orderliness)، استانداردسازی (standardize) و نگهداری (sustain) میشود.
۳) اندازهگیری بهره وری کلی تجهیزات OEE
اندازهگیری بهره وری کلی تجهیزات OEE، به معنای Overall Equipment Effectiveness است و یک معیار عملکرد تجهیزات است که به اندازهگیری بهرهوری تجهیزات تولیدی میپردازد. این مفهوم شامل سه عامل اصلی است: بهرهوری (Availability)، بهرهوری عملیاتی (Performance Efficiency) و کیفیت (Quality) است.
بهرهوری (Availability): نسبت زمانی که تجهیزات قابل استفاده و در دسترس برای تولید است به کل زمان ممکن تولید است.
بهرهوری عملیاتی (Performance Efficiency): نسبت میانگین سرعت واقعی تولید به سرعت استاندارد یا بهترین سرعت ممکن است.
کیفیت (Quality): نسبت تعداد قطعات یا محصولات با کیفیت به کل تولید شده است.
OEE از ضرب مؤلفههای بالا به دست میآید و مقدار نهایی آن نشاندهنده بهرهوری کلی فرآیند تولید است. این معیار به شرکتها کمک میکند تا عملکرد تولید خود را ارزیابی کرده و بهبودهای لازم را ایجاد کنند.
۴) رسیدگی و کاهش تلفات عمده
رسیدگی و کاهش تلفات عمده یا (addressing and reducing major losses) با بررسی محلهایی که بیشترین ضررهای دریافت شدهاند، تلاش برای ریشهیابی مشکل میکند.
در این مرحله از ستون بهبود متمرکز یا کایزن که قبلاً بحث شد استفاده میشود. برای انجام این کار، یک تیم متقابل متشکل از اپراتورها، پرسنل تعمیر و نگهداری و ناظران را گرد همآورید که میتوانند دادههای OEE را با استفاده از تجزیه و تحلیل علت ریشهای تجزیه کنند و علت(های) اصلی تلفات را شناسایی کنند.
۵) اجرای نگهداری و تعمیرات برنامهریزی شده
آخرین مرحله از فرآیند اجرای TPM، ادغام تکنیکهای نگهداری و تعمیرات برنامهریزی شده (implementing planned maintenance) در برنامه شما است. این شامل استفاده از تکنیک پایش وضعیت (Condition Monitoring) است.
به این مقاله چقدر امتیاز میدهید؟
Rating 4.40 from 5 votes
این صفحه را با دیگران به اشتراک بگذارید و امتیاز بگیرید
برای نوشتن دیدگاه باید وارد بشوید.