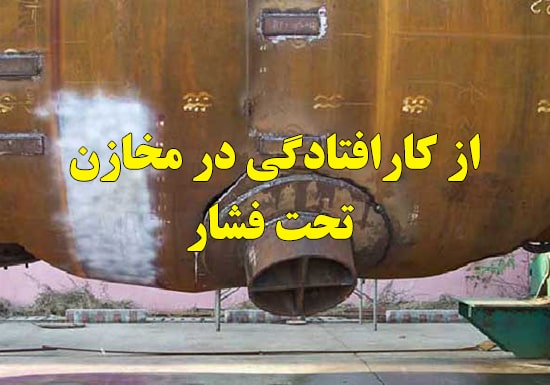
آشنایی با عوامل از کارافتادگی در مخازن تحت فشار
در این مقاله به بحث عوامل از کارافتادگی در مخازن تحت فشار خواهیم پرداخت از این رو توصیه می شود قبل از مطالعه این مقاله ، مقالات پیشین « آشنایی با اصول طراحی و ساخت مخازن تحت فشار » و « اصول بازرسی مخازن تحت فشار به زبان ساده » را مطالعه بفرمایید.
کلمه از کارافتادگی که ترجمه شده کلمه Failure است را این گونه تعریف می کنیم : هرگونه وجود عیب و ناپیوستگی در مخزن که سبب شود نتوان از آن بهره برداری ایمن کرد ، از کارافتادگی نام دارد.
قبلاً در مقاله « اصول بازرسی مخازن تحت فشار به زبان ساده » توضیح داده شد که اگر مخزن در حین کار دچار حادثه شود خسارات جانی و مالی فراوانی را تحمیل می کند لذا باید به نحوی استفاده ایمن از مخازن را برآورده کرد که برای این کار لازم است تا با مکانیزم های از کارافتادگی در مخازن تحت فشار ، آشنا باشیم و بتوانیم آنها را تحت کنترل قرار بدهیم.
مخازن تحت فشار همانند قطعات دیگر در صنایع مختلف دچار از کارافتادگی می شوند. بعضی از این از کارافتادگی ها در اثر فرسایش در طول زمان می باشند و برخی دیگر مربوط به طراحی های نامناسب و مشکلات در زمان تولید و ساخت و بهره بردای غلط از آن می باشند. در دنیای واقعی از کارافتادگی قطعات و تجهیزات امری اجتناب ناپذیر است. به همین دلیل هدف اصلی این باید باشد که حتی المقدور طراحی طوری باید انجام شود که از کارافتادگی در طول عمر مفید قطعه پیشگیری نمود.
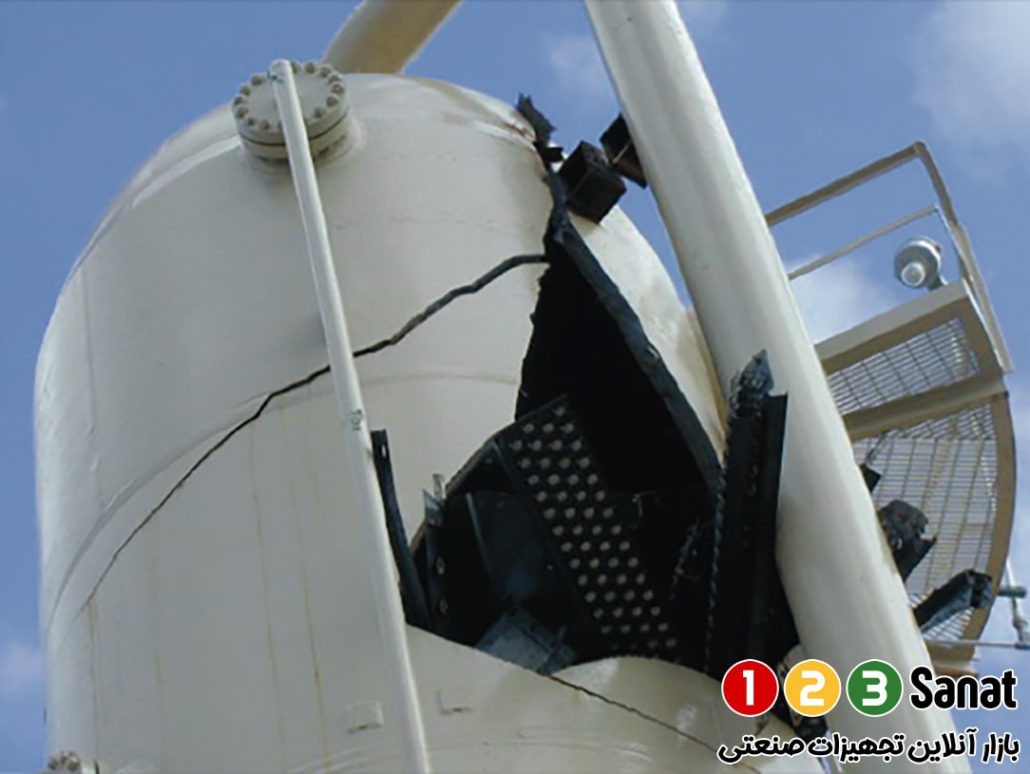
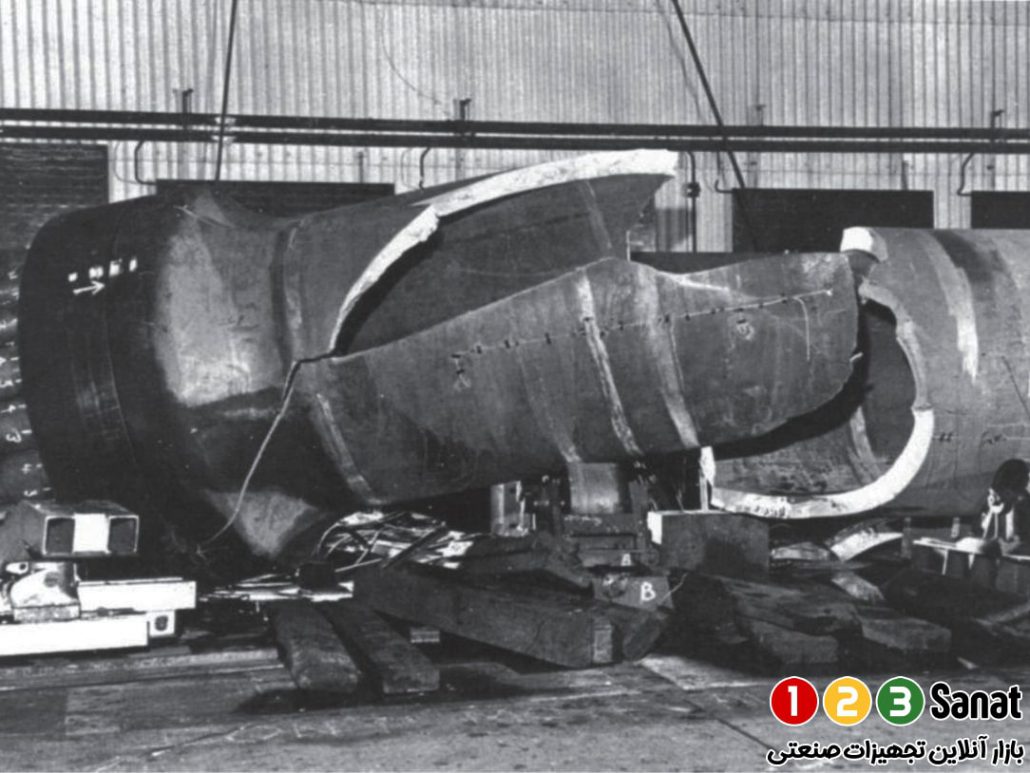
تقسیم بندی انواع از کارافتادگی در مخازن
برای یک طراحی مناسب و قابل قبول باید طراحان این دانش را داشته باشند که از کارافتادگی ها چگونه و به چه دلیل اتفاق می افتند و نهایتاً چگونه می توان از بروز از کارافتادگی های مختلف جلوگیری نمود.
از این رو، استانداردهای مربوطه که بر اساس دانش مهندسی و تجربه در سالیان سال طوری تدوین شده اند که بتوانند تا حد امکان از وقوع کارافتادگی جلوگیری کنند که آنها را در مقاله « آشنایی با اصول طراحی و ساخت مخازن تحت فشار » مورد بررسی قرار دادیم.
فرسایش در مرور زمان در قطعات بسیار رایج است به همین دلیل طراحی باید طوری انجام شود که با در نظر گرفتن شرایط محیطی و اعمال ضریب اطمینان مناسب، احتمال به وجود آمدن قطعه در طول عمر مفید طراحی را تا جاییکه می شود کاهش داد.
اصولاً از کارافتادگی را به دو صورت زیر می توان تقسیم بندی نمود:
۱) از کارافتادگی های که به صورت آنی، بدون بروز علایم اولیه اتفاق می افتند و در اثر یکبار اعمال بار رخ می دهند.
۲) از کارافتادگی هایی که تابع زمان می باشند و به تدریج رخ می دهند.
دسته اول که با اعمال یک بار بار گذاری اتفاق می افتد، بسیار خطرناک هستند که معمولاً ایجاد صدمات مالی و جانی می شوند. این نوع و از کارافتادگی خبر نمی دهند و به همین خاطر بسیار خطرناک هستند. به عنوان مثال اگر فشار داخلی مخزن از حد مجاز خارج شود مخزن دچار انفجار شد باعث صدمات غیر قابل جبران می شود. به همین دلیل بهترین راه برای پیشگیری این است که طراح مناسب انجام شود و ضرایب اطمینان مربوطه در زمان طراحی اعمال شده باشد.
دسته دوم از کارافتادگی ها بر خلاف دسته اول در طول زمان اتفاق می افتند. به عنوان مثال از کارافتادگی خستگی که در اثر بارگذاری متناوب در طول زمان اتفاق می افتد از این دسته از کارافتادگی ها می باشند. این نوع واماندگی ها را می توان با استفاده از بازرسی های خاص و تعمیرات ویژه پیشگیری نمود.
معرفی انواع مکانیزم های از کارافتادگی در مخازن تحت فشار
از کارافتادگی های مختلف که در مخازن تحت فشار می توانند رخ دهند را می توان به صورت زیر تقسیم بندی کرد.
- تغییر شکل بیش از حد الاستیک (Excessive Elastic Deformation)
- تغییر شکل بیش از حد پلاستیک (Excessive Plastic Deformation)
- شکست ترد (Brittle Fracture)
- خزش (Creep)
- رشد سیکلی کرنشی (Strain Cycle Growth)
- خستگی (Fatigue)
- خوردگی (Corrosion)
در ادامه این مقاله سعی می شود تا حد امکان به صورت مختصر هر کدام از مکانیزم های از کارافتادگی را توضیح دهیم.
۱) تغییر شکل بیش از حد الاستیک
تغییر شکل بیش از حد الاستیک یا به انگلیسی Excessive Elastic Deformation که گاهاً به اختصار EED نام برده می شود نوعی تغییر شکل موقت در ماده است که در محدوده الاستیک ماده و در اثر اعمال تنش خارجی به وجود می آید.
دو نوع از تغییر شکل بیش از حد الاستیک ممکن است اتفاق بیافتد: ۱) خیز (Deflection) بیش از حد ماده تحت بارگذاری ۲) کمانش (Buckling) بیش از حد ماده تحت بارگذاری
از کار افتادگی از نوع تغییر شکل بیش از حد الاستیک ، سبب غیرفعال شدن کارکرد سیستم می شود به عنوان مثال یک شفت در داخل یک سیستم مکانیکی را فرض کنید که دچار تغییر شکل بیش از حد الاستیک شده است در نتیجه این شفت می تواند باعث خرابی سریع بلبرینگ ها و یاتاقان ها و همچنین به هم خوردن سیستم تلرانس و انطباقات اجزای جفت (Mating Parts) بشود.
معمولاً تغییر شکل بیش از حد الاستیک در ستون هایی با سطح مقطع باریک و پوسته های جدار نازک اتفاق می افتد. خرابی های ناشی از تغییر شکل بیش از حد الاستیک توسط مدول الاستیسیته کنترل می شود ، نه با مقاومت ماده لذا برای جلوگیری از این خرابی باید ضخامت پوسته یا سطح مقطع تیر را افزایش داد.
تغییر شکل بیش از حد الاستیک ممکن است در مخازن تحت فشار جدار نازک به وجود آید لذا باید تدابیر لازم برای جلوگیری از کارافتادگی در مخازن تحت فشار اندیشیده شود.
۲) تغییر شکل بیش از حد پلاستیک
تغییر شکل بیش از حد پلاستیک یا به انگلیسی Excessive Plastic Deformation که گاهاً به اختصار EPD نام برده می شود ، زمانی اتفاق می افتد که مقدار تنش از حد تنش تسلیم فراتر برود که در این زمان تغییر شکل های ایجاد شده در ماده دائمی خواهند بود. تنش تسلیم ماده عامل تعیین کننده تغییر شکل بیش از حد پلاستیک ماده در بارگذاری تک محوره (Uniaxial Loading) می باشد
تغییر شکل بیش از حد پلاستیک باعث تغییر موقعیت نسبی بین قطعات می شود و کل دستگاه را از کار می اندازد. به عنوان مثال ، شکل دندانه در چرخ دنده در گیربکس (جعبه دنده) که دچار تغییر شکل شده است باعث ایجاد لرزش و سر و صدا و حتی شکستن دندانه می شود که عملکرد گیربکس را مختل می کند.
۳) شکست ترد
شکست ترد یا به انگلیسی Brittle Fracture ، به حرکت سریع و ناگهانی ترک تحت تنش گفته می شود که هیچ گونه یا مقدار بسیار ناچیزی پلاسیسته را قبل از شکست ایجاد می کند. برخلاف از کارافتادگی هایی که به علت اعمال تنش بیش حد به ماده به وجود می آید و مقدار قابل توجهی از تغییر شکل پلاستیک قبل از گسیختگی کامل آن به وجود می آید و هچنین پدیده گلویی شدن (Necking) از شکست قریب الوقوع ماده اطلاع می دهد ، شکست ترد بدون هیچ گونه هشدار قبلی می باشد. دلایل متعددی برای بروز شکست ترد معرفی شده است که برخی از آنها را معرفی می کنیم:
۱) شکست ترد ناشی از دمای پایین ، برخی از مواد مهندسی از جمله فولاد های در دمای پایین رفتار بسیار ترد و شکننده ایی دارند و در مراجع مهندسی دمایی که رفتار ماده از یک رفتار چقرمه به رفتار ترد تغییر وضعیت می دهد دمای انتقال یا Transition Temperature گفته می شود. در مراجع و کد های مرتبط با طراحی مخازن تحت فشار مانند استاندارد ASME VIII طراحان را ملزام کرده است که دمای مجاز بهره برداری مخازن به مقدار قابل ملاحضه ایی بالاتر از دمای انتقال باشد تا جلوی هر گونه از کارافتادگی در مخازن تحت فشار گرفته شود.
۲) تخریب متالورژی ، در برخی از فولاد ها در محدوه دمایی بالا و پایین تر از نقطه ذوب در محدوده ایی بین ۴۰۰ تا ۷۰۰ درجه سانتی گراد در مرزدانه ها عناصر آلیاژی رسوب می کنند که سبب تضعیف شدن ساختار فولاد می شوند برای مثال در فولاد مولبیدن دار جوشکاری شده این پدیده دیده شده است لذا از آنجاییکه از این نوع فولاد برای ساخت برخی از مخازن استفاده می شود لذا باید این مهم را در نظر داشت تا از کارافتادگی در مخازن تحت فشار جلوگیری شود.
۳) خوردگی ناشی از هیدروژن ، در برخی از مخازن تحت فشار نگهداری گاز هیدروژن یا حتی مخازن نگهداری آمونیاک دیده شده است که خطر شکست ترد به علت از دست رفتن چقرمگی بسیار بالا می رود.
۴) سایر عوامل نظیر وجود ضخامت زیاد پوسته ، توسعه تنش های پسماند ناشی از جوشکاری و سایر فرآیند های ساخت خطر ایجاد شکست ترد را بالا می برند.
خزش
خزش یا به انگلیسی Creep یکی دیگر از مکانیزم های از کارافتادگی در مخازن تحت فشار می باشد که فقط در دمای بالا اتفاق می افتد. در پدیده خزش به مرور کرنش و تغییر شکل در قطعه تحت تنش اعمال شده به مرور افزایش پیدا می کند این افزایش کرنش بدون اینکه تنش اعمال شده افزایش پیدا کند در گذشت زمان افزایش پیدا می کند تا قطعه دچار گسیختگی شود.
پدیده خزش ، پدیده پیچیده ایی است که عواملی نظیر دما ، شکل و اندازه دانه ، فاز های تشکیل دهنده و … در آن نقش دارند و به صورت یک قاعده سر انگشتی اگر دمای اعمال شده به قطعه از ۰/۴ دمای ذوب قطعه بیشتر باشد (۰/۴×T>Tm) باید حتماً اثر خزش را در محاسبات گنجاند.
رشد سیکل کرنش
رشد سیکل کرنش یا به انگلیسی Strain Cycle Growth یکی دیگر از مکانیزم های از کارافتادگی در مخازن تحت فشار می باشد که در مخازن نگهداری تحت فشار و سایر انواع مخازن معمولاً همواره اتفاق می افتد. رشد سیکل کرنش معمولاً در اثر ترکیب بارگذاری استاتیک و بارگذاری سیکلی ایجاد می شود.
برای مثال یک مخزن نگهداری تحت فشار را در نظر بگیرید که در روز ۳ بار پر و خالی می شود و در این حین باید تا زمان خالی شدن بعدی سیال را تحت تراکم نگه دارد ، در این شرایط وقتی که مخزن پر و خالی می شود تحت بارگذاری استاتیک و هنگامی که پر و خالی می شود تحت بارگذاری سیکلی قرار دارد.
رشد سیکل کرنش را به صورت های مختلفی می توان نشان داد ، اما یکی از متداولترین روش های نشان دهنده رشد سیکل کرنش روش نمودار بیری (Bree Diagram) است که در ادامه آن را با هم بررسی می کنیم. در این نمودار محور افقی نمایانگر تنش مکانیکی و نمودار عمودی بیانگر بازه تنش حرارتی است . در این نمودار رفتار ماده با ۴ قسمت قابل تفکیک است که در ادامه بررسی خواهیم کرد.
۱) الاستیک : در منطقه الاستیک (Elastic) تنش های ایجاد شده از تنش تسلیم کمتر می باشند و لذا هیچ گونه تغییر شکل دائمی در قطعه به وجود نخواهد آمد و در نتیجه آن از کارافتادگی در این منطقه به وجود نخواهد آمد.
۲) فرود آمدن الاستیک : منطقه فرود آمدن الاستیک (Plastic Shakedown) منطقهایی است که تنش به حد پلاستیک می رسد اما مقدار آن کم است به طوری که بعد از چند سیکل کرنش پلاستیک متوقف می شود و کرنش پلاستیک ثابت می شود که به این حالت فرود آمدن پلاستیک گفته می شود. با لحاظ استاندارد های طراحی رسیدن سطح تنش ها در داخل قطعه به اندازه قرار گرفتن در منطقه فرود آمدن الاستیک بدون مشکل است.
۳) رشد سیکلی کرنش : رسیدن حد تنش ها به طوریکه منجر به رشد سیکلی کرنش (Ratcheting) بشود بسیار خطرناک است چرا که کرنش پلاستیک به ازای هر سیکل رشد خواهد کرد و این رشد تا مرحله گسیختگی پیش می رود. با لحاظ استاندارد های طراحی رسیدن سطح تنش ها به منطقه رشد سیکلی کرنش بسیار خطرناک است و باید به صورت جد از آن جلوگیری کرد.
۴) بار نهایی : در منطقه بار نهایی (Collapse) همانطور که از نام آن پیدا کرد سطح تنش ها به قدری بالا است که تنها یک سیکل بارگذاری برای گسیختگی کامل قطعه کافی است. طراحان باید تدابیر لازم برای پیشگری از این واقعه را بیاندیشند.
خستگی
خستگی یا به انگلیسی Fatigue ، به پدیده مستهلک شدن قطعه در طول زمان گفته می شود. در خستگی به مرور زمان در قطعه ترک های بسیار ریزی به وجود می آیند که به مرور توسط اعمال تنش رشد می کنند و این رشد تا گسیختگی کامل قطعه آدامه خواهد داشت.
در کدها و استاندارد هایی که برای طراحی مخازن تحت فشار ارائه شده است از نظر بررسی پدیده خستگی به دو رویکرد قابل تفکیک است.
۱) عدم نیاز به تحلیل خستگی : طبق شرایطی مانند سطح تنش پائین و دامنه تنش کم و … می توان از تحلیل خستگی مخزن طرف نظر کرد.
۲) الزام به انجام تحلیل خستگی : در بیشتر مخازن که کاربرد صنعتی دارند استاندارد مربوطه طراح را ملزم کرده که در محاسبات خود پدیده خستگی را بگنجاند.
خوردگی
خوردگی یا به انگلیسی Corrosion یکی دیگر از مکانیزم های از کارافتادگی در مخازن تحت فشار می باشد که باید مد نظر قرار داد. خوردگی انواع مخلتفی دارد که بسیار جای صحبت دارد اما ساده ترین نوع خوردگی که قابل ذکر است خورده شدن جداره مخزن و کاهش ضخامت آن می باشد. بدیهی است که جداره مخزن با توجه به شرایط مسئله و سطح تنش های موجود در مخزن در نظر گرفته شده است و چنانچه بروز خوردگی سبب کاهش ضخامت پوسته شود شرایط را می تواند بسیار وخیم کند.
لذا یکی از مواردی که در کدها و استاندارد های مخازن تحت فشار که به منظور بازرسی مخازن تحت فشار مانند استاندارد ASME XI مورد تاکید قرار گرفته است این است که همواره با استفاده از تست های غیر مخرب NDT ، ضخامت جداره مخزن تست شود.
به این مقاله چقدر امتیاز میدهید؟
Rating 4.36 from 11 votes
این صفحه را با دیگران به اشتراک بگذارید و امتیاز بگیرید
برای نوشتن دیدگاه باید وارد بشوید.