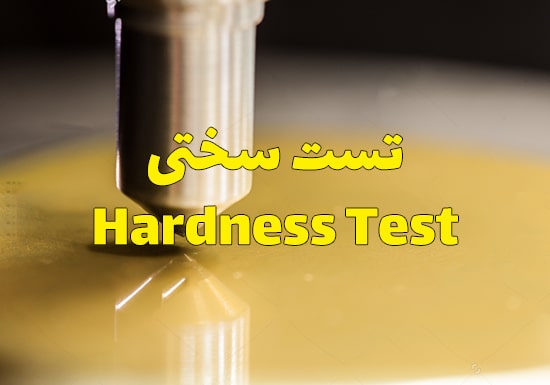
صفر تا ۱۰۰ تست سختی و کاربرد آن در جوش
سختی یا به انگلیسی Hardness به معنای مقاومت جسم در برابر فرورفتگی است. بدست آوردن مقدار سختی یک نمونه با استفاده از تست سختی انجام میشود که تعدادی روش برای این مهم وجود دارد مانند: سختی برینل (Brinell Hardness)، سختی ویکرز (Vickers Hardness)، سختی راکول (Rockwell Hardness)، سختی نوپ (Knoop Hardness)، سختی شور اسکلروسکوپ (Shore Scleroscope Hardness) و… که در این مقاله به سختی برینل، ویکرز و راکول، خواهیم پرداخت.
تست سختی برینل
تست سختی برینل و به انگلیسی Brinell Hardness Test، برای اولین بار توسط یک محقق سوئدی به نام یوهان آگوست برینل در آغاز قرن بیستم ابداع شد.
این آزمایش شامل فشار دادن یک توپ فولادی سخت شده به سطح نمونه با استفاده از یک بارگذاری استاندارد و ایجاد یک فرورفتگی بر روی سطح است؛ همانطور که در شکل زیر نشان داده شده است.
نسبت قطر فرورونده به بارگذاری (diameter/load ratio) یک مقدار مشخص است؛ در این تست قطر فرورونده و مقدار بارگذاری به ترتیب میتواند بین ۱ تا ۱۰ میلیمتر و ۳۰ تا ۳۰۰۰ کیلوگرم باشد که این مقدار برای فلزات مختلف استاندارد شده است. برای مثال برای فولاد این نسبت ۳۰: ۱ است برای نمونه یک توپ ۱۰ میلیمتری را میتوان با بار ۳۰۰۰ کیلوگرم یا یک توپ ۱ میلیمتری با بار ۳۰ کیلوگرم استفاده کرد. برای آلیاژهای آلومینیوم این نسبت، ۵: ۱ است. باید در نظر داشت که بار برای مدت زمان ثابتی اعمال میشود که معمولاً ۳۰ ثانیه است. هنگامی که فرورفتگی ایجاد میشود، دو قطر قالب، d۱ و d۲، با استفاده از یک میکروسکوپ با یک گرتیکول مدرج (calibrated graticule) اندازهگیری میشود و سپس همانطور که در شکل زیر نشان داده شده است، میانگین میشود.
عدد سختی برینل (BHN) که مخفف Brinell hardness number است با تقسیم بار بر مساحت سطح ایجاد شده، بدست میآید. انجام این محاسبات ممکن است تا حدودی خستهکننده باشد لذا برای سادگی محاسبه مقدار سختی، مجموعهای از جداول استاندارد که از روی آنها میتوان مستقیماً عدد سختی برینل را خواند ایجاد شدهاند.
فرمول محاسبه سختی برینل، در شکل زیر نشان داده شده است که در آن P، مقدار بارگذاری است. مقدار D و d به ترتیب قطر ساچمه و مقدار میانگینگیری شده قطر اثر ابزار بر روی سطح میباشد.
تست سختی برینل کمتر تحت تأثیر زبری سطح قرار میگیرد زیرا مقدار حاصل میانگین دو مقدار است با این حال به دلیل قطر بزرگ ساچمه کروی، آزمایش نمیتواند برای تعیین تغییرات سختی در یک اتصال جوشکاری شده استفاده شود و برای آن معمولاً از تست ویکرز استفاده میشود. فلزاتی که سختی آن بیش از ۴۵۰BHN میباشد ممکن است باعث تغییر شکل فرورونده کروی و در نتیجه خواندن نادرست شوند. برای غلبه بر این محدودیت، فرورونده کروی کاربید تنگستن به جای ساچمه فولادی سخت شده استفاده میشود، اما محدودیت سختی ۶۰۰BHN نیز با این فرورونده نیز وجود دارد.
تست سختی ویکرز
تست سختی ویکرز به انگلیسی Vickers Hardness Test، بر اساس اصول مشابه تست برینل عمل میکند. تست سختی ویکرز در سال ۱۹۲۱ میلادی توسط رابرت ال اسمیت و جورج ای سندلند در شرکت ویکرز لیمیتد (Vickers Limited) ابداع شد. تفاوت عمده تست ویکرز با برینل استفاده از یک فرورونده الماس هرمی شکل مربعی به جای یک فرورونده کروی فولادی سخت شده است. همچنین برخلاف تست برینل، عمق برداشت تأثیری بر دقت قرائت ندارد بنابراین نسبت قطر فرورونده به بارگذاری (diameter/load ratio) مهم نیست. الماس در بارهای زیاد تغییر شکل نمیدهد، بنابراین نتایج روی مواد بسیار سخت قابل اطمینانتر است. در این تست بارگذاری ممکن است بین ۱ تا ۱۲۰ کیلوگرم باشد و زمان اعمال نیرو بین ۱۰ تا ۱۵ ثانیه باشد.
همانطور که در شکل زیر نشان داده شده است، دو وجه هرم مربعی شکل d۱ و d۲، اندازهگیری شده و مساحت سطح محاسبه شده و سپس به بار اعمال شده تقسیم میشوند.
همانطور که قبلاً ذکر شد، فرورفتگی ویکرز کوچکتر از فرورفتگی برینل است و بنابراین میتوان مناطق بسیار کوچکتری را آزمایش کرد، که امکان انجام بررسی در سراسر یک اتصال جوش داده شده، از جمله اجراهای جداگانه و مناطق تحت تأثیر حرارت HAZ را فراهم میکند. برداشت کوچک همچنین به این معنی است که سطح باید صاف و عمود بر جسم فرورونده باشد لذا باید سطح قبل از اندازهگیری سنگ زده شود.
فرمول محاسبه سختی ویکرز، در شکل زیر نشان داده شده است که در آن P، مقدار بارگذاری است. مقدار L، مساحت فرورونده هرمی شکل میباشد.
تست سختی راکول
تست سختی راکول به انگلیسی Rockwell Hardness Test، بر اساس اصول مشابه تست برینل و ویکرز عمل میکند، تفاوت عمده آن استفاده از نوع شکل فرورونده با توجه به جنس نمونهها میباشد که در ادامه بحث خواهد شد. تست راکول توسط هیو ام راکول و استنلی پی راکول در سال ۱۹۱۴ برای ارزیابی کیفیت عملیات حرارتی بلبرینگها ابداع شد.
تست سختی راکول، در طبقهبندیهای مختلف با حرف لاتین قرار میگیرند که مقدار ظرایب آنها و مقدار بارگذاری با توجه به نوع تست سختی راکول متفاوت است اما به صورت کلی شکل فرورنده در راکول C ،A و D هرمی شکل و در راکول F، B و G کروی شکل با قطر ساچمه ۱/۱۶ اینچ (۱.۵۹ میلیمتر) و برای راکول E قطر ۱/۸ اینچ (۳.۱۸ میلیمتر) است.
فرمول سختی راکول، به صورت HR=N-hd است که مقدار h و N ضرایب ثابت این تست هستند که با توجه نوع تست راکول مشخص میشوند و d مقدار نفوذ فرورونده به داخل نمونه است. مقدایر ثابت را در جدول زیر مشاهده میکنید.
طبقه بندی | مخفف | بارگذاری برحسب کیلوگرم-نیرو (kgf) | هندسه فرورونده | کاربرد | N | h |
---|---|---|---|---|---|---|
A | HRA | 60 | هرمی شکل | فولاد نازک، فولاد کم عمق سخت شده | 100 | 500 |
B | HRB | 100 | کره ۱/۱۶ اینچ | آلیاژهای مس و آلومینیوم، ، فولادهای نرم و چکش خوار | 130 | 500 |
C | HRC | 150 | هرمی شکل | فولاد و چدنهای سخت، فولاد چکش خوار پرلیتی، تیتانیوم، مواد دیگر سخت تر از 100 HRB | 100 | 500 |
D | HRD | 100 | هرمی شکل | فولاد نازک و متوسط سخت شده | 100 | 500 |
E | HRE | 100 | کره ۱/۸ اینچ | چدن، آلیاژهای آلومینیوم و منیزیم، فولاد بیرینگ، پلاستیک گرماسخت | 130 | 500 |
F | HRF | 60 | کره ۱/۱۶ اینچ | آلیاژ مس آنیل شده، ورق های نرم و نازک | 130 | 500 |
G | HRG | 150 | کره ۱/۱۶ اینچ | برنز فسفر، مس بریلیم، آهن های چکش خوار. | 130 | 500 |
H | HRH | 60 | کره ۱/۸ اینچ | آلومینیوم، روی، سرب | 130 | 500 |
K | HRK | 150 | کره ۱/۸ اینچ | آلیاژ بلبرینگ، قلع، مواد پلاستیکی سخت | 130 | 500 |
L | HRL | 60 | کره ۱/۴ اینچ | آلیاژ بلبرینگ و سایر مواد بسیار نرم | 130 | 500 |
M | HRM | 100 | کره ۱/۴ اینچ | ترموپلاستیک ها، آلیاژ بلبرینگ و سایر مواد بسیار نرم | 130 | 500 |
P | HRP | 150 | کره ۱/۴ اینچ | آلیاژ بلبرینگ و سایر مواد بسیار نرم | 130 | 500 |
R | HRR | 60 | کره ۱/۲ اینچ | آلیاژ بلبرینگ و سایر مواد بسیار نرم | 130 | 500 |
S | HRS | 100 | کره ۱/۲ اینچ | آلیاژ بلبرینگ و سایر مواد بسیار نرم | 130 | 500 |
V | HRV | 150 | کره ۱/۲ اینچ | آلیاژ بلبرینگ و سایر مواد بسیار نرم | 130 | 500 |
15T, 30T, 45T | —– | 15, 30, 45 | کره ۱/۱۶ اینچ | برای پوشش های نرم- سطحی | 100 | 1000 |
15N, 30N, 45N | —– | 15, 30, 45 | فرورونده براله (Brale indenter) با الماس مخروطی ۱۲۰ درجه و شعاع نوک ۰/۲ میلی متر | برای مواد سخت شده-سطحی | 100 | 1000 |
خطا در تست سختی
عوامل زیادی وجود دارد که میتواند بر دقت تست سختی تأثیر بگذارد. که در ادامه به برخی از آنها اشاره خواهیم کرد.
۱) صافی و پرداخت سطح در رسیدن به نتایج درست بسیار مهم است لذا باید قبل از انجام تست سنگ زنی یا ماشین کاری لازم، انجام شود.
۲) وضعیت فرورفتگی بسیار مهم است؛ در حالی که الماس ویکرز به ندرت خراب میشود مگر اینکه به صورت ناشیانه از آن استفاده شود، توپ برینل در طی یک دوره زمانی تغییر شکل میدهد و نتایج نادرست ایجاد میشود.
۳) مسطح بودن سطح بسیار مهم است؛ حداکثر زاویه تقریباً ۱± درجه قابل قبول است.
۴) ابعاد نمونه مهم است؛ اگر قطعه آزمایش خیلی نازک باشد، بر روی نتیجه تأثیر میگذارد. برای آزمایش برینل، حداقل ۸ برابر عمق آزمایش توصیه میشود و برای آزمایش ویکرز، حداقل ضخامت دو برابر قطر باید باشد.
۵) فاصله فرورونده از لبهها باید مقدار کافی باشد؛ اگر فرورونده بسیار نزدیک به لبه نمونه باشد، مقادیر سختی کمتر ثبت میشوند؛ لذا حداقل فاصله باید حدود ۴ تا ۵ برابر قطر فرورونده از هر لبه آزاد باشد.
کاربرد تست سختی در جوش
برای اینکه از ایمن بودن یک سازه جوشی اطمینان حاصل شود و از بروز فجایعی مانند شکست سازههای جوشی جلوگیری شود بسیار مهم است که خواص جوش مورد آزمایش قرار بگیرد. برای جوشکاری برخی فلزات مانند جوشکاری آلومینیوم و برخی از فولادهای آلیاژی، کدها و استانداردهای جوشکاری مربوطه سازنده را ملزم به انجام تست سختی میکنند. پدیده افت سختی پس از انجام جوشکاری برخی از آلیاژها میتواند سبب بالا بردن ریسک تخریب سازه جوشی شود لذا مهم است که برای برخی از فلزات تست سختی برای تائید WPS جوشکاری توسط مهندس جوش انجام شود. انشا.. در آینده این مباحث به صورت کامل در دوره مهندسی جوش بحث خواهند شد.
تبدیل سختیها به یکدیگر
شاید برخی از افراد سؤال بپرسند که آیا رابطه یا فرمولی وجود دارند که بتوان با استفاده از آن واحدهای سختی را به یکدیگر تبدیل کرد؛ به عنوان مثال سختی برینل را به ویکرز یا راکول C را به برینل و…. تبدیل کرد؟
پاسخ منفی است؛ به علت تفاوت ماهیت هر کدام از تستهای سختی و تفاوت در نوع شکل فرورونده و همچنین فرمول محاسبه سختی معادل، نمیتوان رابطهایی را برای این مهم ارائه کرد.
در برخی از کدها و استانداردها معادل مقدار سختی برای دو تست متفاوت آمده است که در ادامه آنها را بررسی میکنیم.
استاندارد BS ۸۶۰: ۱۹۶۷ که امروزه توسط BS EN ISO ۱۸۲۶۵: ۲۰۰۳ جایگزین شده است، معادله زیر را برای تبدیل سختی بین مقیاسهای برینل و ویکرز ارائه میدهد.
HB = ۰. ۹۵ x HV
در برخی از فعالیتهای کارگاهی سختی راکول C را با ویکرز، مرتبط کردهاند و گفتهاند به صورت تقریبی ۲۲ راکول C تقریباً معادل ۲۴۸ ویکرز است. برخی از سایتها به صورت تقریبی برای شما سختی معادل را بدست میآورند که باید توجه داشت مقادیر ذکر شده به صورت تقریبی است؛ یکی از این سایتها «سایت تبدیل مقایسهای سختی به یکدیگر» که میتوانید از لینک داده شده به آن مراجعه کنید.
به این مقاله چقدر امتیاز میدهید؟
Rating 3.53 from 19 votes
این صفحه را با دیگران به اشتراک بگذارید و امتیاز بگیرید
برای نوشتن دیدگاه باید وارد بشوید.